Aspen Pittman: Behind the Gear with Groove Tubes
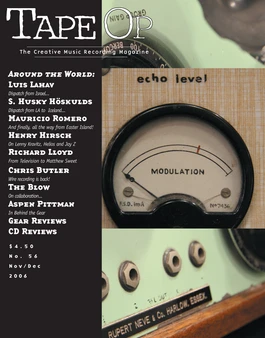
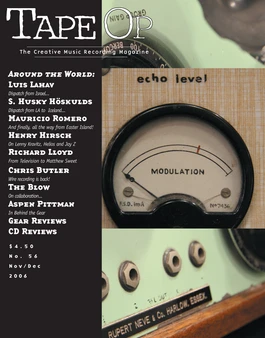
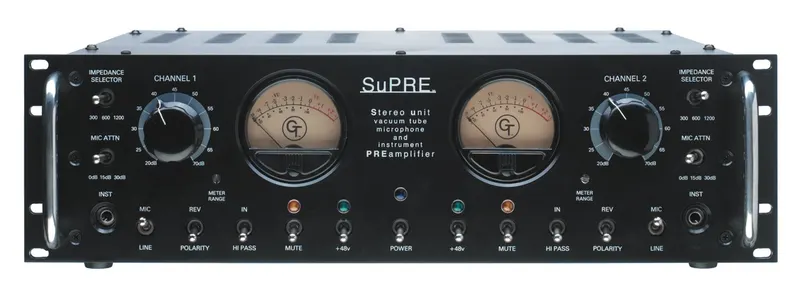
The name Aspen Pittman is synonymous with vacuum tubes. But it's one thing to hawk a product, and another to understand the physics behind its performance. While working as a salesman in the first Guitar Center store, Pittman noticed that players (and techs) didn't really know why there were wide sonic differences between identical tube amps. He suspected the tubes, but there was little known then about matching power tube pairs or selecting prime preamp tubes for replacement. His curiosity eventually led to inventing a whole new standard for matching guitar amp tubes β one that works. Today, you'll hardly find a professional guitarist who doesn't have a set of Groove Tubes in his amp. Likewise, Pittman's Groove Tube uniquely designed pro audio products are found in world-class facilities around the globe. We caught up with Aspen Pittman at this year's TapeOpCon. We wanted to know about a little more behind the gear...
The name Aspen Pittman is synonymous with vacuum tubes. But it's one thing to hawk a product, and another to understand the physics behind its performance. While working as a salesman in the first Guitar Center store, Pittman noticed that players (and techs) didn't really know why there were wide sonic differences between identical tube amps. He suspected the tubes, but there was little known then about matching power tube pairs or selecting prime preamp tubes for replacement. His curiosity eventually led to inventing a whole new standard for matching guitar amp tubes β one that works. Today, you'll hardly find a professional guitarist who doesn't have a set of Groove Tubes in his amp. Likewise, Pittman's Groove Tube uniquely designed pro audio products are found in world-class facilities around the globe. We caught up with Aspen Pittman at this year's TapeOpCon. We wanted to know about a little more behind the gear...
A lot of people know you from your Tube Amp Book.
We've had a lot of success with The Tube Amp Book. I believe the first printing was around 75,000 copies, and since then we've printed another 20,000 of the revised Deluxe Tube Amp Book. So, we're nearing 100,000 copies.
That's significant in this industry.
Yes, it's a lot of books in this industry. And to think there are that many people interested in what makes tube amps work, what makes tubes work and how to make them better. I never expected this level of interest in tube amps.
How did you even get involved in tubes?
I went to work for the first Guitar Center in Hollywood during their very early days β about six months after they'd opened their doors. There were only older organ store salesmen there β I was the first longhaired employee under 40 that could also tune a guitar! Six months later I was made manager at just 19 years old!
A lot of guys get into music retail, but that doesn't mean they end up as a manufacturer. What got you involved in electronics?
Well, my knowledge until then was just acoustic instruments, but now I had to learn about the electric guitar and amps. I noticed we would get an amp in and it wouldn't sound quite right, so we would send it to the repair shop. The amp came back as "okay". So nothing was "broke", but it still didn't sound right. I then learned about "tubes" and the improvements I could make by just simple substitution. I discovered that much like strings, tubes wore down (but didn't actually "break" like strings). So you didn't notice your loss of tone as the tubes wore out until it was too late (i.e. "My amp blew up!"). But guys were not replacing worn tubes until it was in the shop, and then only the one that went out. Basically this situation began my quest to figure out the contributing factors to what would be considered a "good" Marshall 100 or a "good" Fender Twin Reverb. I knew tube amps relied on tubes, an electrical component possessing great influence on the sound, so that was a good place to start researching. I found the tubes in new amps were very inconsistent, hence explaining the vast differences in amps as we unpacked them. So the amp's tone, good or bad, was due to the luck of the "tube draw" at the factory. So the question became, "How do we create a situation where there will always be a good tube draw every time?"
But didn't they measure tubes at the amp or tube factories?
Well yes, and no. Most amp factories bought tubes from the distributors of RCA or GE parts and those tubes indeed "met spec", which is a series of "minimum electrical measurements". Indeed the tubes worked, so the amp was passed, but still they all sounded a bit different. Amp companies knew nothing about testing and/or "matching" their tubes, and since nothing was "broken" they didn't try to fix it. But I knew something here was "broken", and I saw the opportunity for a possible business if I could produce better sounding amps thru installing better sounding tubes. My initial inspiration was McIntosh Laboratory, who made high- end, tube-based home stereo gear. McIntosh used to put on tube amp clinics with their dealers, where owners would bring in their Mac amplifiers and then factory techs would measure them and (if needed) recommend new "matched tubes" from the factory. We measured the trans-conductance (or the power) of a tube and matched them accordingly into sets... just like McIntosh. But there was one small problem.
What was that?
When you listened to the amp with our electrically matched tubes it didn't sound any better, at all! I was disappointed because unless I could prove this idea to the picky ears of a guitarist, I knew I had no product to market. My tubes needed to sound better, so I knew we still had more research to get where I wanted to be.
But they were matched, right?
Yes, and no. These first sets were matched the old way. You have to remember, tubes as we were using them in guitar amps were never designed to be "tone generators", so nobody was looking at their individual "tone". Instead, they were designed to be an amplifier stage, or just to make power. They were more typically used as receivers of radio signals, which was a very different application. So power and transconductance testing might be the correct way to match tubes depending on your application, but we found it useless for making better sounding amps. We then reasoned that tubes in a guitar amp are a part of the musical producing process in and of themselves. We started looking at matching tubes from a "tone generation" standpoint. We thought, "Let's not measure their power; let's measure their transfer functions, hence their musical contribution." We started measuring a tube's harmonic distortion character that is audible and we hit pay dirt β they varied a lot in this area β so we started matching the "X factor". For discussion, let's call it 5% THD [Total Harmonic Distortion] threshold. We would put a signal in a typical guitar amp circuit and drive a single tube until the tube reached a 5% distortion level. At that point, we would take a power reading and convert that into a rating system we could "match". We had created a gain-to-distortion ratio... and this was the basis of our future company.
Did that reveal anything?
We found out an interesting thing. Let's take an example of a 6L6 tube, which will put out about 20 watts. In the old system of power matching, one 6L6 would be 19 watts, others 21 and some 20... and we would match them by output. But as I said, you cannot hear small differences in power, so this didn't really work. It takes double the power to hear just a 3 dB output change, but you can hear 5% THD easily. We found out that over a 20-watt range, some 6L6 tubes were generating meaningful harmonic structure at 50% of their output say, 10 watts, while other 6L6s might not show anything until 18 watts!
So, how is this threshold important to tone?
Think about it β if you have one tube that turns over at 50% output and another that doesn't until 90%, you have two tubes that do not sound the same. They are resonating differently, and you'll get phase cancellation. And that can be note specific. You could have a big sustain in midrange frequencies like the D and G strings, but the low E and high E just die. That is a type of phase cancellation in the amp. You could go nuts trying to tune up your guitar, but it's not in the guitar, it's happening in the amp. So instead of focusing on power, we began to focus on this "musically meaningful" factor. We call it gain-to-distortion ratio, and so we have a 1-10 rating scale for our matched tubes that goes from early distortion (#1) to late distortion (#10, with more headroom if you want that). So finally we could offer tubes that are "musically" matched" (that is from a tone generation standpoint), and the amp was noticeably improved... so we had a product and officially started our company back in 1979.
I thought I knew a lot of about tubes and now I feel like a complete moron.
We all blindly accept and repeat the story of how tubes, when driven into distortion, create a low-order, second- order harmonic distortion that is pleasing, whereas a solid-state device will generate a third-order, high-level harmonic that is disturbing. Now, this was commonly thought to be the whole reason we liked tubes. But that's a great example of measuring something that does not matter, explaining the differences between tubes and transistors... at least for pro audio. It also showed there were things that did matter that we were not able to measure β back then at least. When digital recording came in, we were about complete in making the overall transition from tube gear to solid-state gear for the front- end signal path. The AKG [C] 414 mic replaced the AKG C 12A tube mic. In consoles we had the sleek Neve console instead of the big tube desks and outboard, tube-based preamps and processors. Before digital, all these new devices were being used with tape media. And as we now know, tape saturates and masks the dynamic range of a processing device. But with digital, we gained all of this dynamic range, and with it the ability to expose dynamic range issues like never before. All of a sudden we had the ability to observe, with our ears, wider dynamic ranges. That's just when everyone rushed back to tubes chanting, "We need tubes to warm up that cold digital recording." That is what everyone assumed, that digital recording was cold, but they were really hearing cold transistors in the front-end components. So tube gear sounded better to the new ears digital recording gave us. The observations were correct, tubes were better sounding (most agree) and the confirming THD measurements were easy to prove, but the conclusions were absolutely wrong. Everyone assumed that we wanted to hear second order distortion, tubes had it and transistors didn't. In fact, the opposite was true. Tubes technically distort far less in those ways "that matter" in the dynamic content of the signal! Think about it β if tube devices like U47s and U67s and Pultec EQs generated gobs of second-order THD, something in the 4 to 5% range, they would sound awful. But all these devices measure in the point zero range!
Are there any other key factors?
Well, the big measurement "that mattered" had a lot to do with our perception of sound, and it's a signal's dynamic distortion character, or lack thereof. When CDs first came out, I hated the way drums and cymbals sounded... so thin, unlike my vinyl records. Dynamic distortion is at play here, not just headroom. See, the dynamic transfer function is at play. Today we have much faster, computer-based measurement devices to test dynamic distortion, and now we find tubes have VERY low levels of dynamic distortion. But solid-state devices have tons of it β IC op-amps more so than FET devices (isn't it interesting that most engineers prefer FET circuitry for it's "warmth"?). Digital recording isn't cold; it's really more neutral. But all of a sudden, with the expanded dynamic range of digital recorders, we could finally hear (and later measure) the high dynamic distortion levels of those nasty solid-state devices (and lack thereof in tube gear). Tape machines used to disguise it, cover it in saturation. But now, with an ADAT, a U87 didn't sound as good as the U67 tube version, the 414 not as good as the C 12A. In a nutshell, tubes don't distort in "ways that matter" β yet in ways that "don't matter" they aren't as "technically perfect" as a transistor.
So how did this get into recording gear and tube microphones?
There was a time early on in the GT saga when I went in as a technician for the Doobie Brothers, who were recording over at Alley Studios in North Hollywood. I changed the tubes in Pat Simmons' tweed Bandmaster using my new GT tubes, matched to my specs. The engineer ran out saying, "What did you do to that amp?" My first thought was I was in trouble, but I quickly realized he was happy and amazed. He said, "I can pull all of my compressors because it's so smooth now." The differences I had heard were even more dramatic on playback, and we wound up re-tubing every amp the Doobies had... and they are still loyal GT users after nearly 30 years! That was the day I got interested in recording. There are so many parallel lessons that can be transferred from my experience with perfecting tubes, musical instruments and their tube amps, and the various chains in the studio signal chain. In Groove Tubes mics we chose tubes that have a much lower filament current, which generate less heat and hence less noise (and we select them for low microphonics and hum). We also work with balancing impedance characteristics of the various stages (much like amps to speakers), both in matching the capsule to the electronics and the transformer to the front of the board or preamp. The active circuitry in a tube microphone is primarily for impedance conversion β getting the signal not so much louder, but way down in pipe size from where it started (i.e., from 2 billon Ohms down to a few hundred), and with that much math to be done, there is a risk of loosing frequency response, or worse, harmonic distortions. You can easily degrade the signal by an increase of harmonic distortion, but perhaps most importantly, you can loose dynamic realism β a naturalness that is there in the capsule is often lost in the following electronics. There was an article in Tape Op where David Royer took an inexpensive "meatball Chinese" mic, did some "mods" (basically substituting some more expensive USA parts in the signal path) and the mic's sound improved greatly. It shows the point that electronics in a microphone cannot be "additive", but they do have the potential to degrade the signal, as with the cheap Chinese components in Royer's Chinese mic... Royer's mod was not "additive", but it prevented the subtraction of tone and the capsule was allowed to breathe new life. However like electric guitars, with a mic, the real rubber meets the road with its transducer β the element that transforms thin air into voltage. Its sound is much less dependent on the following electronics. So we put most of our time, money and effort into our transducers. For example, GT was the first to offer a 3- micron diaphragm capsule, which is half as thick as everyone else at that time (and still is for the most part!). That was not easy β by contrast the tube circuitry was relatively easy for us after so many years in the tube business! The more effort you spend to make a better transducer, the better your overall sound will be. We've refined our capsule manufacturing process and chosen quality components. Our most critical signal path parts are either made by us here or imported to our Shanghai factory from various Western countries. That allows us to make mics they way they used to be made, in the old, labor-intensive process, but using modern (and better) components. The cost of a condenser mic is more than 50% in the labor, and ours are no exception; we spend 20 to 25 hours assembling, tuning and tensioning, heat curing and stabilizing our capsules. This extra work insures they stay reliable, consistently "matched" and sounding incredible for years to come. For example, making a common cardioid mic is fairly easy, as it's only a one-sided affair and needs no special consistency matching. But for multi-patterned capsules that must have two sides, it is quite a different challenge. To get quality results, the two single-sided capsules must be perfectly matched...and that is not cheap or easy. So when you slap these two-faced capsules back to back and flip the phase, you'd better have correct 180-degree cancellation or you won't get a perfect figure-8 pattern. The only way for a perfect 180 is to make every capsule EXACTLY the same, so both sides are closely matched when assembled together. In fact, our construction standards needed to be so tight that our capsules' sensitivities are consistent to +/- 1.5 dB at full bandwidth. In order to make perfect dual-sided capsules, we had to develop our own designs, materials and manufacturing processes. Right out of the box, any two same model GT mics are matched pairs! And they are closer than most of the aftermarket "matched pairs" offered by some of the most famous brands for increased cost. So then it was also a natural evolution to go from making tubes to making microphones and on to tube- based studio gear... where we have products in the obvious market segments.
What pulled you into the microphone business?
People came to us concerned that the U87 was selling for $1,500, but similar tube Neumann mics were selling for $5,000. They were getting an extra $3,500 for adding a single tube. Well that sounded like it could be a good business for us! We were making high-powered tube guitar amps with a dozen tubes and large transformers with even larger speakers that sold for less that half an imported tube mic! We got a team of good guys β musicians and engineers β and started to make the first GT MD1 tube mic. We used an off-the-shelf Primo electret capsule from Japan. We made a simple tube output stage, added a Reichenbach output transformer (Tom's company is now called CineMag) and we came out with the world's first modern $1,000 tube mic that many say was our best ever β though I disagree: we got much better as we began to make our own, true condenser 3 micron capsules and went to smaller format tubes!
That sounds cool, but how did you go from making a few mics a month to becoming a global manufacturer?
GE was selling their tube line and closing the US factory. So, I saw this as a great opportunity. I took my collection of vintage tube amplifiers and sold them to Guitar Center. They went for an average of $1,000 each, and there were about 250 of them. I took the money, bought the factory machines, materials and processing formulas for the GE 6L6 and GE 6CA7 and began the adventure of making tubes, starting at the component level. That was an investment in our core business that has yielded benefits for all our tube-based products.
How did doing these different things work out for you as a business owner?
Well, I learned it's not easy to dance at three weddings. I had an aftermarket tube company for guitarists, a pro audio company for recording engineers and a new SFX patent to develop (stereo from a single box) and that was just starting out. That's when Alesis approached me and offered to buy my recording division. This allowed me to concentrate on what I do best (my core business was/is still tubes), and they could do what they did best with my GT mics β the recording business. Of course various things happened after that transaction, and two years later Alesis was going out of business. But before they went out of business I was able to get my intellectual property back (in trade for my unpaid debts) and during the liquidation I was also able to purchase the Groove Tube inventory and was back in business in fairly short order. Then I secured a two-year agreement with Guitar Center to exclusively distribute the mics, and we developed a few there like the GT Convertible (which just won the TEC award). Now GT mics are back in general distribution, but I could not have managed that with out Guitar Center stepping in and giving me a lot of good business so I could get this division back on its feet.
What are you doing in terms of the product lines?
In the recording market we have polarized products. At one end we have the Brick that "streets" for $400, and on the other end we have the ViPRE, which is a no expense-spared device and streets around $3,000. So, now we're trying to fill the gap between, and we just introduced a large format stereo tube preamp that will street for around $1,500 called the SuPRE (Stereo Unit PREamplifier).
What's next for Groove Tubes Microphones?
There will be a new large format multi-patterned edge terminated capsule soon (tentatively called GT88), our soon-to-be released VELO-8 ribbon mic and some stereo offerings as well. Also we will introduce a fixed- head version of the GT Convertible (a hand-held vocal mic whose head removes for guitar and drum applications) that we call the "Hardtop". Both of these true condenser hand-held mics street for around $100 and sound amazing! We're also working on a passive equalizer that's going to have some very flexible control options, 64 ways to passively EQ your signal path (has no nasty coils or inductors, only tubes/caps/resistors). It will be called VARI-X.
You're not going to reissue an old EQ?
For the ViPRE we had to make its knobs, meters and switches, and we introduced variable impedance loading to expand any mic's applications. Almost nothing on our boxes is "off the shelf". Also, it's hard to improve on a Fairchild compressor or an original Neumann tube mic! I would rather be held accountable for my own original designs than be compared to a reissue of another company's masterpiece!