Billy Woodman started ATC in 1974 and was trying to advance the art and science of building high performance speaker drivers. Is that correct?
Ben Lilly (Ben): Yes. He'd been working at Goodmans [a British loudspeaker firm], and he had a few ideas for drive units whilst he was there. During that time, Goodmans was going in a different direction towards higher volume, lower margin commercial-type products. The ideas he had around that time for a 12-inch PA driver, and also the initial idea of what would go on to become the 3-inch ATC soft dome midrange, were very much high quality, higher price type products. Goodmans weren't very interested, so he decided that he'd forge off and do his own thing. So that's when ATC was founded. The bread and butter there was the drive units for the live sound industry. A 12-inch, to begin with, then I think a 15-inch, and then a 9-inch driver. The studio and the hi-fi field were in the background. What ran the company and paid the bills at that time were the drive units for the live sound. It would have been late-'70s or early-'80s when we put together our first three-way system, the S50, which then evolved to become the SCM50, which we're still making today. That's been in continuous production since the early '80s.
Brad Lunde (Brad): It'd probably be an interesting point to add that this whole thing happened around the time manufacturers making speakers learned that they could get a better price if they bought OEM [original equipment manufacturer] parts from somebody else and had their own internal manufacturing. If you research what JBL looked like in the '60s, it's not all that different from the way that ATC looks now, where they were handmaking everything. Once companies got into the higher volumes, they needed to find a way to lower the cost.
When you say OEM, you mean that companies are buying parts that they didn't make, putting them in a cabinet, and selling it?
Brad: Right. The challenge of that, of course, is that you can only buy what's available. There are manufacturers today that will custom-make you a driver, but there's a limit to that. They can't invest hundreds of thousands of dollars in your personal pet project if it won't pay the bills. They have to write off any engineering they do on the product that they sell you. There's a limit to what you can get these OEM companies to do. That's where ATC began, of filling that niche by having something different than what was available from everyone else.
The simple way to put it would be that ATC wanted to build everything in-house.
Ben: That's where Billy came from. When he was at Goodmans, they were still doing it that way. From coil-winding all the way through. That's what he knew. If you were an engineer then, it wasn't the case that you took the glory job of the actual final system design and the listening tests. You were working on everything. You're looking at the raw materials, the drawings, tolerances, making sure everything fits together, and that clearances are correct. Not the drive units themselves, but the raw components the drive units were actually made from, all the way to the finished system. Billy got that experience at Goodmans, and then he took that on to ATC. At that time, we wanted to do ribbon-wire voice coils – you can buy that wire now, but you couldn't buy it then. Billy had his brother make the machine to flatten the wire we were using. There weren't machines available from suppliers to do the edge-wound voice coils, so we had Billy and his brother work on developing the winding machines for those voice coils. There's a lot that goes into it. I suppose, from a customer point of view, they just see the finished product; but there's an awful lot of process and detail behind that finished product. For ATC, the drive units, the components in it, are the most important thing. If you're engineering a system, that defines what the system's going to do. You can still poorly engineer a system with great components, but you're never going to engineer a great system with poor components.
When I went looking for new monitors, I was looking for a company that did research and development to build their own drivers and then design everything to work together from the ground up, as opposed to somebody buying drivers built elsewhere, amplifiers built elsewhere, and then throwing them in a box.
Ben: When you properly have a look, there're not too many companies doing it anymore. Probably less every year. But the drive unit development, and the amplifier development, and building it all in-house is the heart of the company.
I went to John Rodd's studio [Tape Op #107] before this, and I heard his system, which is very impressive. He said that with the midrange driver that what you're hearing is exactly what you're going to hear when you get the smaller speakers.
Ben: I think, going back to when ATC was founded, Billy identified early-on to build a better speaker, a better midrange device, was going to be vital. He's also a piano player and that drove that development. Piano's a difficult instrument to reproduce; [especially accounting for] wide bandwidth and dynamic with a lot of harmonic content. It's a challenge to reproduce. He was never happy with what was around in the '70s and that drove the development of a better speaker. He identified that a better midrange driver was the crux of doing that. At that time, we had these hi-fi systems in the UK that had great fidelity, but they didn't have any dynamic range. In the U.S., you had all of these systems that were born from cinema and, with all due respect, lacking a little bit of fidelity, but still capable of tremendous dynamic range. That drove the development of that midrange driver that took the best of what was available in the U.K. and the U.S. High dynamic range and outstanding fidelity, i.e., low distortion. Billy, through testing, also identified that we would need something that would produce a big sound field if it was to be successful in a professional market.
Wide dispersion?
Ben: Yes. We need a nice big sound field. You don't always want to sit dead center. You need to be moving around, equalizing and balancing. The part also needed to be relatively small if it was going to spread sound over a nice, wide pattern. He came up with the idea of using a dome device, driven at its edge, so you'd have maximum voice coil size but keeping the diaphragm size relatively small.
Right. Well, it works!
Ben: It's also a similar diameter to your mouth and how the sound disperses from your mouth and your head as well. I think that may have some influence on why it sounds natural when you're listening to it.
Yeah. Have you ever got to hear just one of the midrange drivers being run, without the tweeter and woofer?
Ben: Yes. Through the crossover, it does sound quite band-limited, but there's still an awful lot of information there. That's probably another key. We cross it over at 380 Hz and 3.5 kHz, so it's doing nearly a full decade. Of course, an ideal loudspeaker would be a single point source. But if you want dynamic range, good bass extension, and good high-frequency extension, it is impossible. We need to go to a multi-driver system. If we're going to go to a multi-driver system – with the midrange being key and relating so much information, with guitars, pianos, and voices – if we can get it to cover as wide a bandwidth as possible and push those crossover frequencies away from that critical mid-band where our hearing's more sensitive as well, we're on the way to getting a good result.
I'd assume that crossover device technology has been an ever-expanding quest for as much accuracy as possible?
Ben: Yes, though we've had a couple of changes. Early on, we went active. I think we were developing active in late-'70s or early-'80s, and then the first commercial active systems would have been about '83 or '84. Getting rid of the passive crossover is a massive step. It's quite an inelegant thing to work with, and a little restrictive. When you're trying to optimize the passive crossover design, you're often having to make a bit of a compromise, whether it's in the frequency response, or the phase, or the impedance. You're always pinching from Peter to pay Paul. You can improve one parameter and lose the other. If you go to active crossovers, we've got independent control of the timing aspect, the phase, the rollout, and the shape. You can achieve much greater accuracy, and more affordably. A 3-way passive crossover is an expensive thing to build well. You end up with a far more accurate system with the active design. An active system will always sound tighter, more dynamic, and faster in the low frequency than its passive equivalent.
What year did the ATC start doing powered monitors?
Ben: It would be early '80s. Properly up and running, the active 50s would have been about '84 or '85.
Brad, when did you come aboard and start working with ATC in the U.S.?
Brad: I didn't start with ATC until 2002 or 2001. I was there right as they introduced the last generation of tweeter. They had a smaller line then. We had 20s and then it skipped up to 50s, 100s, and 150s. We didn't have much in between a small 2-way and this big 3-way that was the 50.
I should mention that all these numbers we're giving out are the cubic liters of the cabinet.
Ben: Yes, the size of the cabinet in liters.
Right. When did the SCM25A show up?
Ben: We launched them at the AES Show in 2009.
Now there's a much wider range than ever of sizes, right?
Ben: The 25 and 45 are the products where we've filled in. We identified that there was a big gap in the middle of the range. It was 20 to 50, and now, for the active speakers, we go 20, 25, 45, 50. The 50s have the 9-inch bass driver and then the SCM100 with the 12-inch, 110 with the dual 9-inch, 150 with the 15-inch. You've got a very similar drive unit and amplifier technology across that whole series of products. Then, above the 150, you go to the SCM200s and the 300s where the differentiator there is that, typically they are mounted in-wall, and the speakers are driven by an outboard amplifier.
Right. ATC also builds an external amplifier, right?
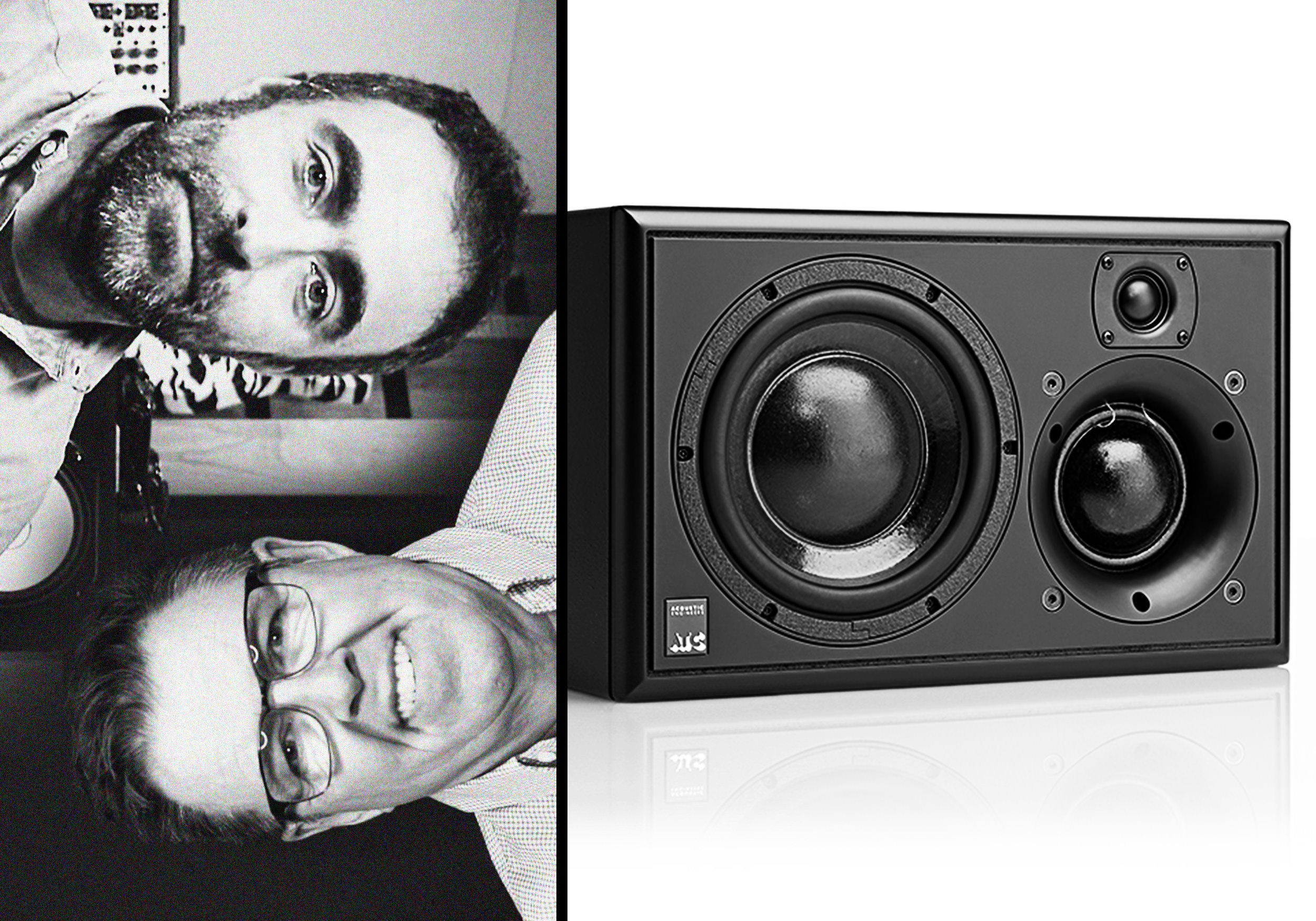
Ben: Yes. Everything up to the SCM150 employs a standard on-board amp. We've got remote amps rack kits for these situations where the speakers are mounted in-wall. 200s and 300s are only used with the P4 amplifier, which is a 5U, 19-inch, fan cooled rackmount product.
At this point, what's the lowest cost ATC monitor someone could have for a studio?
Ben: We've got the SCM12 Pro, which is a passive 2-way design.
Brad: It's $1,850 in the U.S. for a pair of those.
Ben: A 6.5-inch driver with 1-inch tweeters in a 1.5 cubic foot cabinet.
When someone looks at some of the passive, smaller monitors, what do you recommend for amplifiers on those?
Ben: Well, we make our own amp, the P1 Pro, but it's not cheap, and I can appreciate that many home studio people might not be able to stretch to it. I'm in a luxurious position of not having to use any other amplifiers, so I haven't gotten any brilliant recommendations.
Brad: Well, there's a lot of used amps out on the market.
Ben: A secondhand Bryston would work brilliantly, and they're pretty bulletproof.
Is there anything in the future from ATC we should be looking out for?
Ben: There're no new product developments we can talk about at the moment, but there's always work going on in the background, covering all aspects of our product range. Drive unit engineering, and trying to improve the components. That's where we feel we can make big improvements, with the drive unit components themselves. When we get to the point where we feel we have a significant update, or multiple smaller updates, available, we'll launch a new version or sometimes make a rolling change.
Brad: The last introduction you did was a new tweeter, right?
Ben: Yes, a new tweeter was launched in 2014, which updated the products from the SCM50 through to the SCM150.
Brad: We can also upgrade an older speaker with these newer tweeters.
Ben: That's right. Were possible, we try to make older products upgradable wherever possible. Sometimes it's not possible for mechanical reasons or cost, but, in many cases, the older products can be updated. Everything's built to be serviced. We're still servicing some of those Mk1 SCM50s that come back to the factory now.
What are some of the notable studios we would find ATCs in at this point?
Ben: Sterling Mastering in New York and Nashville. Brad's probably better with all the U.S. clients.
Brad: In L.A. the major studios – United Recording and EastWest Studios – they're all heavily ATC-equipped. The Village has SCM25As and Ed Cherney's room had SCM45A's. Blackbird Studios is probably one of the first major studios that went ATC. Then you have a lot of studios where the engineers bring the monitors they want with them. There are a lot of cases to buy SCM25As for that very reason.
I know Thomas Jouanjean at Northward Acoustics [Tape Op #135] uses ATCs exclusively in his room designs. I've heard his Telegraph Mastering room here in town that my friend, Adam Gonsalves, runs.
Ben: Thomas has been a big supporter. He works with other products as well, but he likes the results he gets with the ATCs. We love the work that he does with his rooms. There are a couple of nice Northward spaces that'll be completed in the next six months that we're excited about. One Atmos room, in particular.
Ben: What has been your experience, Larry, working with the SCM25As?
Jackpot!'s control room is about 15 1/2 ft. by 33 ft long, with almost 12-foot ceilings. It's treated by happenstance, not by professional design. I never felt my previous monitors really worked in this room. The day that these arrived from Brad, I was tracking a band for basic sessions. Some of the players from The Decemberists were in the band. Between actual takes, I swapped out the monitors. They had been coming in and listening, and then going back in and tracking. The drummer, John Moen – whom I've worked with ever since I opened over 25 years ago, said, "Oh, the toms sound better!" I hadn't touched the console at all. I'd barely even had a chance to set these speakers up. I said, "That's exactly what I was looking for." These work better in my room. People sitting on the couch in the back of the room here have less odd things to say about the mix.
Ben: Like I said, the dispersion's wide. The low frequency goes everywhere, regardless, unless the speaker's enormous or it's flush-mounted, which gives it some directionality. If you then have a beamy, directional midrange, then you get this weird imbalance of the energy in the room. It could be some of the broad dispersion characteristic helping that evenness of balance over a bigger space in the room.
Everything started working better after getting these monitors. It's hard to write a review and explain that, but the sessions went smoother.
Ben: Hopefully you didn't have to think about the speakers anymore. I suppose that's the goal. If the room and the monitors are good, you forget about it and get on with your work. That's the best it can be.
I have NS10s and the Avantones here. They don't usually get powered up when I'm mixing alone. I have a [Dangerous] Monitor ST; it remains set at a level and I get to work.
Brad: What's it like for you, over the course of the day? Is it the same? Do you find that when you start in the morning, you're getting the same results late in the day?
Yeah. I don't notice any difference. I don't burn out on these monitors. It's nice having the subwoofer. I get about everything I need, except a tiny bit of low end extension off the SCM25As.
Ben: That's nice to hear. When we set out to design that product, we wanted the majority of people to be happy with the bass extension without a sub for most situations, so hopefully we've achieved that goal.
Brad: It's interesting when you talk to people. If they don't have a lot of experience as an engineer, they want a speaker that sounds good. When you talk to somebody who's got a lot of experience, they want a speaker that shows them what's wrong.
Ben: It makes life easier, as well. You don't want to be acting as an agony aunt [an advice columnist]. You want to be getting on with the recording and mixing.