Behind The Gear at Purple Audio. Photo 01 of 22 Behind The Gear at Purple Audio. Photo by Pete Weiss www.weissy.com Behind The Gear at Purple Audio. Photo 02 of 22 Behind The Gear at Purple Audio. Photo by Pete Weiss www.weissy.com Behind The Gear at Purple Audio. Photo 03 of 22 Behind The Gear at Purple Audio. Photo by Pete Weiss www.weissy.com Behind The Gear at Purple Audio. Photo 04 of 22 Behind The Gear at Purple Audio. Photo by Pete Weiss www.weissy.com Behind The Gear at Purple Audio. Photo 05 of 22 Behind The Gear at Purple Audio. Photo by Pete Weiss www.weissy.com Behind The Gear at Purple Audio. Photo 06 of 22 Behind The Gear at Purple Audio. Photo by Pete Weiss www.weissy.com Behind The Gear at Purple Audio. Photo 07 of 22 Behind The Gear at Purple Audio. Photo by Pete Weiss www.weissy.com Behind The Gear at Purple Audio. Photo 08 of 22 Behind The Gear at Purple Audio. Photo by Pete Weiss www.weissy.com Behind The Gear at Purple Audio. Photo 09 of 22 Behind The Gear at Purple Audio. Photo by Pete Weiss www.weissy.com Behind The Gear at Purple Audio. Photo 10 of 22 Behind The Gear at Purple Audio. Photo by Pete Weiss www.weissy.com Behind The Gear at Purple Audio. Photo 11 of 22 Behind The Gear at Purple Audio. Photo by Pete Weiss www.weissy.com Behind The Gear at Purple Audio. Photo 12 of 22 Behind The Gear at Purple Audio. Photo by Pete Weiss www.weissy.com Behind The Gear at Purple Audio. Photo 13 of 22 Behind The Gear at Purple Audio. Photo by Pete Weiss www.weissy.com Behind The Gear at Purple Audio. Photo 14 of 22 Behind The Gear at Purple Audio. Photo by Pete Weiss www.weissy.com Behind The Gear at Purple Audio. Photo 15 of 22 Behind The Gear at Purple Audio. Photo by Pete Weiss www.weissy.com Behind The Gear at Purple Audio. Photo 16 of 22 Behind The Gear at Purple Audio. Photo by Pete Weiss www.weissy.com Behind The Gear at Purple Audio. Photo 17 of 22 Behind The Gear at Purple Audio. Photo by Pete Weiss www.weissy.com Behind The Gear at Purple Audio. Photo 18 of 22 Behind The Gear at Purple Audio. Photo by Pete Weiss www.weissy.com Behind The Gear at Purple Audio. Photo 19 of 22 Behind The Gear at Purple Audio. Photo by Pete Weiss www.weissy.com Behind The Gear at Purple Audio. Photo 20 of 22 Behind The Gear at Purple Audio. Photo by Andy Hong Behind The Gear at Purple Audio. Photo 21 of 22 Behind The Gear at Purple Audio. Photo by Andy Hong Behind The Gear at Purple Audio. Photo 22 of 22 Behind The Gear at Purple Audio. Photo by Andy Hong
How'd you get your start doing Purple Audio?
I was lucky to go to a high school with a really good music program. We had a Yamaha RM1608 console, a Tascam MS16 1-inch, 16-track, and a bunch of Sennheiser MD 421 mics — pretty good equipment for a high school. I was a saxophonist in the second jazz band, and I ended up doing a lot of front-of-house sound. Also, some of the band guys would hang out with me, and we'd just record. Little by little, I got into electronics — fixing and making cables, then building headphone breakout boxes and a distribution system. Then I wanted to go to college for music and recording. I went to NYU for one of their music programs in the mid-'90s. I was bored, immediately. I already knew a lot of what they were teaching freshman year. I started interning at a studio, and that was okay, but I quickly realized I didn't have the personality to be a studio engineer. I didn't want to hold anybody's hand or stroke anybody's ego. A guy named John Klett came into the studio to help with a grounding problem. John took everything out of the console — he wanted to mount a copper bar inside the whole length of the console. I don't know if Middle Atlantic made the copper bar that had the 10 32 holes in it at the time, but I wasn't aware of it. John either didn't know about it, or thought it would be funny to have me make my own — I'm not sure. It was a 1/2'' by 1/2'' copper bar, and I drilled and tapped around 80 holes. I was kind of embarrassed, because I broke some of the taps into the holes. John was like, "How many did you break?" I said, "I don't know. Four or five?" He said, "That's it? You did good. It's hard to tap copper." At the time, I was making a little money buying and selling junk — searching through the classified ads, going out to Long Island and buying gear, coming back in and selling it somewhere else. Then I ran into, "Oh, I bought this thing and it's broken. I'd better learn how to fix it so that I can get my money out of it." One of the first ones was an Eventide H910 Harmonizer. Luckily the guy at Eventide I called was really nice and patient with me. I was just beginning to understand enough about electronics to know what I was looking at. An H910 is not the thing to start with; there's an incredible amount of parts in there. Anyway, I fixed a couple and got my money back out of them. When Sam Ash Parts was moving out of their space on 7th Ave into the space across the street, Manhattan Audio wanted a bigger space. John went in with them; I went in with John and started getting into repair. They were doing a lot of work — keyboards, ADAT machines, and TASCAM 388 consoles with the reel-to-reels in them. John was into Neve modules, Telefunken gear, tape machines, and all that. People were bringing in PYE compressors and things you wouldn't get to buy or see, unless it was in for repair. There was either no schematic, or you'd reverse engineer it. At some point, I was working on UREI 1176s. I was looking at them thinking, "You paid $2,500 for this?" This was '96 or '97. The 1176 sounds cool, but it wasn't built that well. It was built for permanent installation in a rack for the rest of its life, not bouncing around on the road or schlepped from studio to studio. It was structurally deficient. Component-wise, it was great for the time. But you can build way better stuff now. I came out with the Purple Audio MC76 and showed it at the '97 AES show. I started with those and sold them for a while. We outgrew the shop, and I found an old theater building in Queens that had been converted into a nightclub called Exile in the '70s. I rented this 7,000 sq. ft. theater on the second floor. We were able to rip apart a whole console, spread out a tape machine, and actually do the work in a way that was impossible at the midtown location. We shared that shop with Matt Marinelli of Coral Sound until I left New York in 2007.
How much of your business, now that you're in Jim Thorpe, is repair versus manufacturing?
When I left New York, I was basically done with that part of the business. Repair kept me going, especially during slow times. When Universal Audio re-entered the market, business was terrible for me for a while; I had to do console refurbs and tape machine repairs just to keep living. When the UA 1176 was re-issued, I took the MC76 and added the true bypass and insert loop — some features to make things a little bit more modern.
That was the MC77, right? What was your next product?
The Biz preamp [Tape Op #55]. I had wanted to get into the 500-series before. I'd already started making this little rackmount mixer. It was a 1-inch format mixer, so I was looking for an input transformer that would fit in a 1-inch space. I settled on the Lundahl 1550. I started messing with that [circuit] and realized that we had a really cool mic preamp. That was the offshoot that became the Biz. In the standard Class A Neve gear, there's a third gain stage that turns on at 65 dB. It's a whole different sound than at 55 dB. I liked that concept, but I wanted to be able to control it. The Biz has a Dual button that throws in an additional gain stage after the first input stage; it changes the whole character. A dual-deck pot varies the gain of both input stages, at the same time. An output level control allows the Biz to get more aggressive, or less aggressive, as you go forward and backward on the gain and level controls. A lot of the preamps coming from Neve modules didn't have a fader on them anymore. You had gain, but that was all you had. Going to tape or DAW was hard, because you'd have that certain sound, but then your level would be wrong, unless you put an attenuator on it. After the Biz, I came up with another preamp called the Pants. There are four op-amps in there running fully differential throughout. It has a custom CineMag transformer that was made for a mic output. It uses an interesting winding method. It's kind of the same dual-bobbin type as a Lundahl 1550. I like the sound of it. It distorts in a crazy way — very harmonically. The Lundahl in the Biz also distorts. The odd harmonics are really interesting when you drive the hell out of it. I had some low-frequency distortion problems on the 1550s I was getting from Lundahl at some point. I called Per Lundahl up and he said, "Oh, that's not a mic input." I said, "The turns are right for a mic input." He said, "Yeah, but you shouldn't be using that for a mic input. I make much better mic input transformers. Try these." They were all boring. I didn't like them, so I kept the 1550. I still buy them from Lundahl, and Per still laughs when he sees me at trade shows. He comes over to me and says, "Still using that wrong?" It's fine. It sounds great.
I've noticed, in the products you're manu-facturing now, there's modularity in the design. You can pull some of these daughter [expansion] cards out, for example.
My repair background very much makes me think about how I fix things. For example, almost all of my designs have DIP-8 sockets beneath the discrete op-amps. I'd never seen anybody do that before. I'd be sitting there working on a Neve module back in the day, be it a discrete 440, or whatever op-amp, wishing I could just plug something in and see if everything else worked so that I wasn't chasing five different problems. Being able to pull out one of my discrete KDJ 4 op-amps and put in a TL071 — it doesn't sound like you want it to sound, but I know the whole thing works now. Now I just have this one building block that I can either repair or replace, whatever it is.
How many 500-series products do you make now?
We have eight 500-series modules, as well as the Sweet Ten Rack [Tape Op #100]. The Action is a compressor, with similar characteristics to the MC77 and 1176. It has wider attack and release times, so you can do some more dramatic things, like the Eventide Omnipressor "backwards drums" kind of sound. We make three different EQs. The ODD and TAV [Tape Op #77] were designed by Ed Anderson, and they're takeoffs from an Auditronics 501 console project he sucked me into. The inductor EQ on that console was cool, but it was surrounded by junk. If you actually gave it some headroom, as well as good op-amps and transformers, it sounded cool. That became the ODD; it's a big improvement. The TAV was kind of the same thing in a 10-band graphic — all inductor-based. The LILPEQr is a program EQ, designed by Jens Jungkurth from Eisen Audio. He made some with old Neve parts before he ran out of parts. It's a cool EQ, so we made it into a Purple Audio product. The Moiyn module [Tape Op #100] is a mixer module that turns the Sweet Ten Rack into an 8×2 mixer. You can cascade them together and make bigger systems.
Did you give up on making a full console?
No, I designed a couple of consoles. There's one in New Jersey; a Blue Man Group guy has one in his basement. It has 32 inputs, five auxes, and two 2-buses. Then I designed a 500-series console; I have an aux router done and a bus router done for it, and they're expensive as hell. But nobody's going to buy a $50,000 console from me; it's not the brand. So I took that and started designing our MF system. The MFtwenty5 is an analog, discrete, dual-input single-rackspace 10×2 with mute, solo, and pan. Each channel can be switched mono or stereo. You can stack 500-series modules on top of each other and do left/right vertically, and you're able to build a pretty compact 20×2 stem mixer. You could also plug your DAW directly into the MFtwenty5 instead; it's just standard D-subs. It's all digitally controlled — over a thousand SMD [surface-mount device] components to do all the switching. The digital side was all programmed by Jon Ulrigg of ShinyBox [Studio Electronics]. It's been a long road to get this thing to be a viable product, partly because I was overconfident of how my muting and switching was working. Part of it was getting the ethernet to do what I want it to do. I wanted to be able to link them, control them externally, and automate them — I jumped into everything optimistically! Otherwise I wouldn't start projects. I'm halfway through redoing this building, and if I had known how much work it would be, I wouldn't have started it.
How often do you record here?
I've recorded almost every live music show at the Opera House for the last few years — over 200 shows. I bought this building because it's attached to a huge, beautiful live room that I don't have to heat, own, or pay taxes on. My pitch to the bands is simple: come on a Monday or a Tuesday, stay in town all week, record whatever you want, set up, do a live show Friday night, and then get out of here Saturday morning. The Opera House draws crowds. People come from far away. There's no other town like this, with a venue like this. Also, Purple Audio is next door; we're recording the show, and it's totally stress-free.
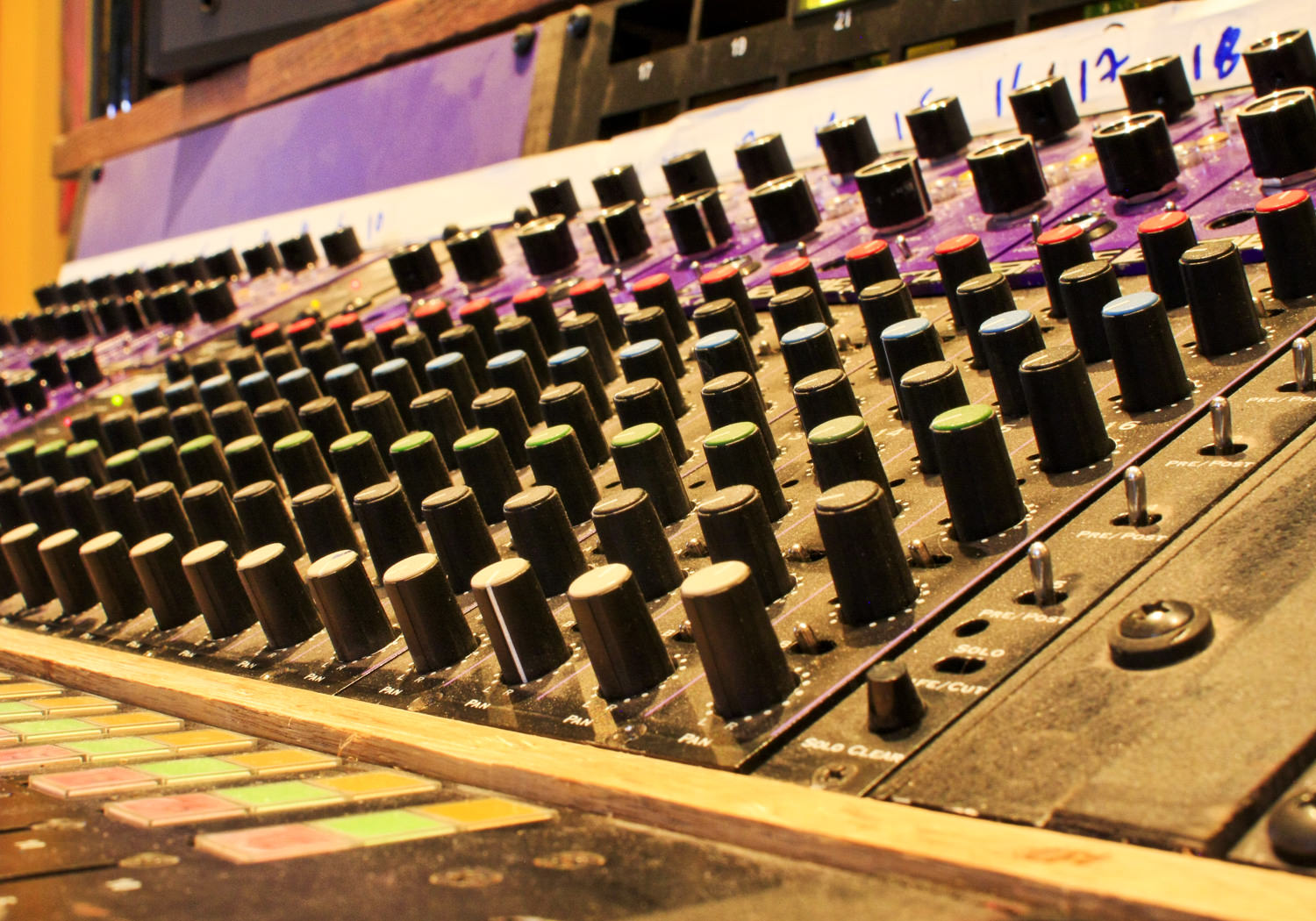
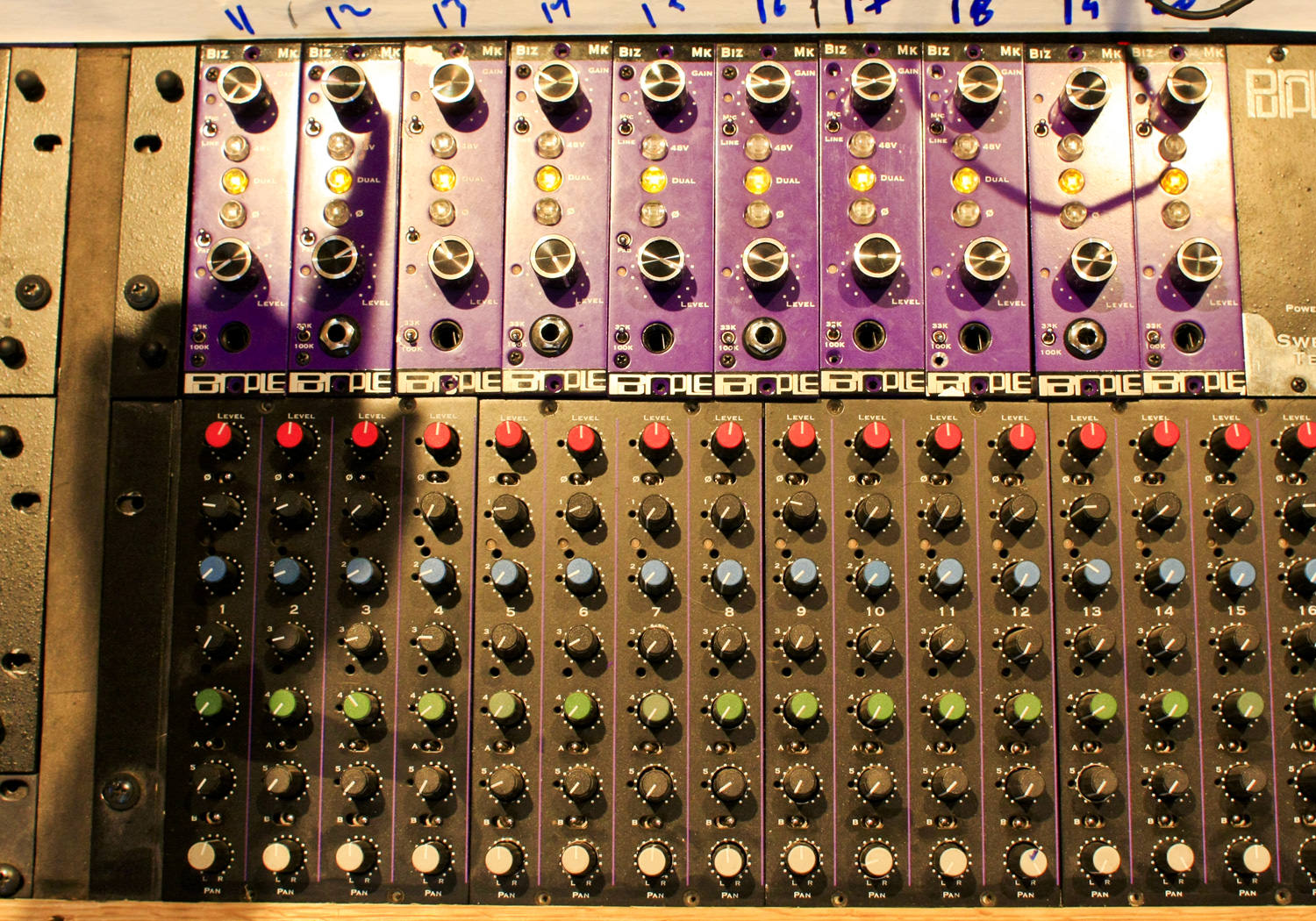
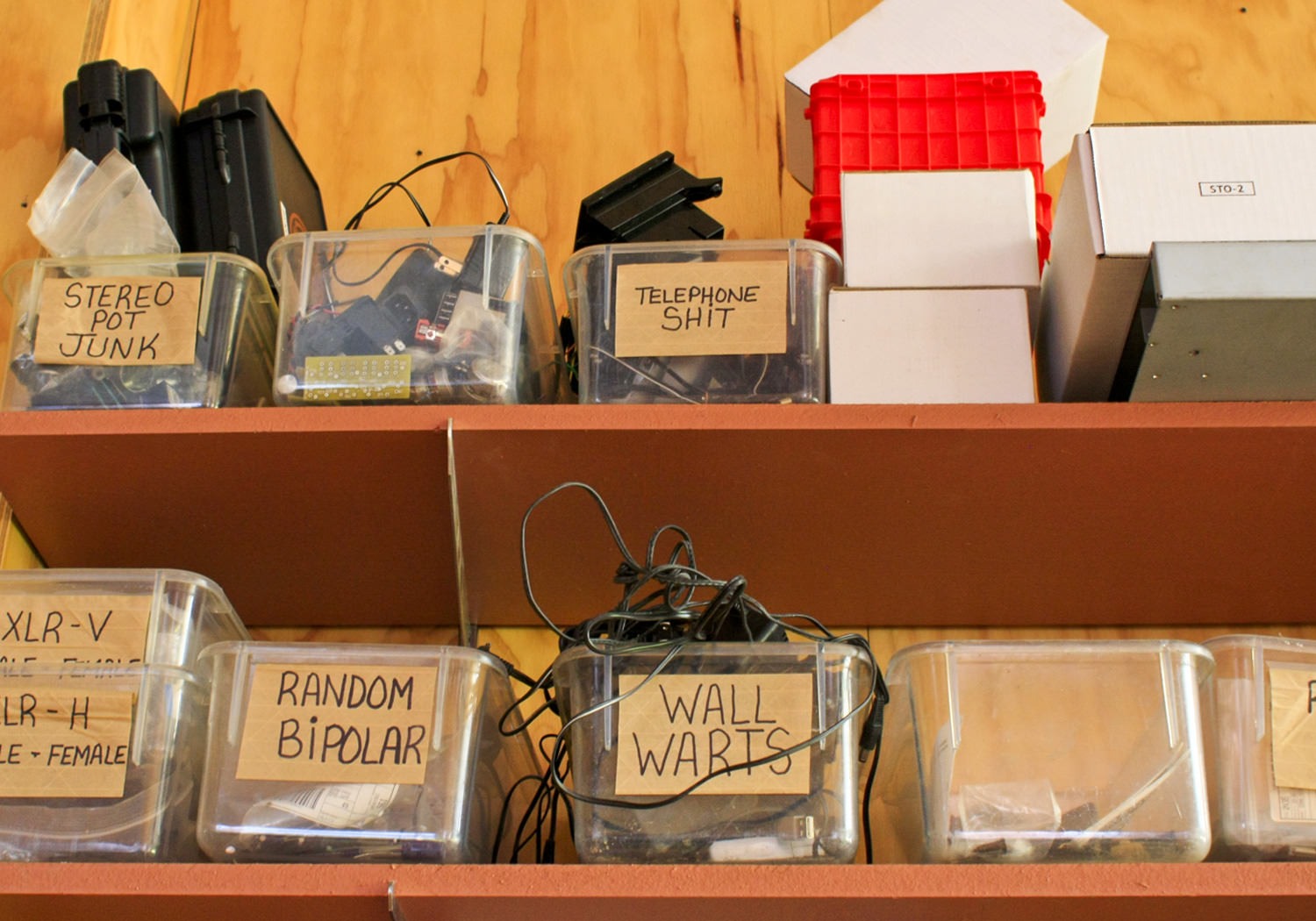
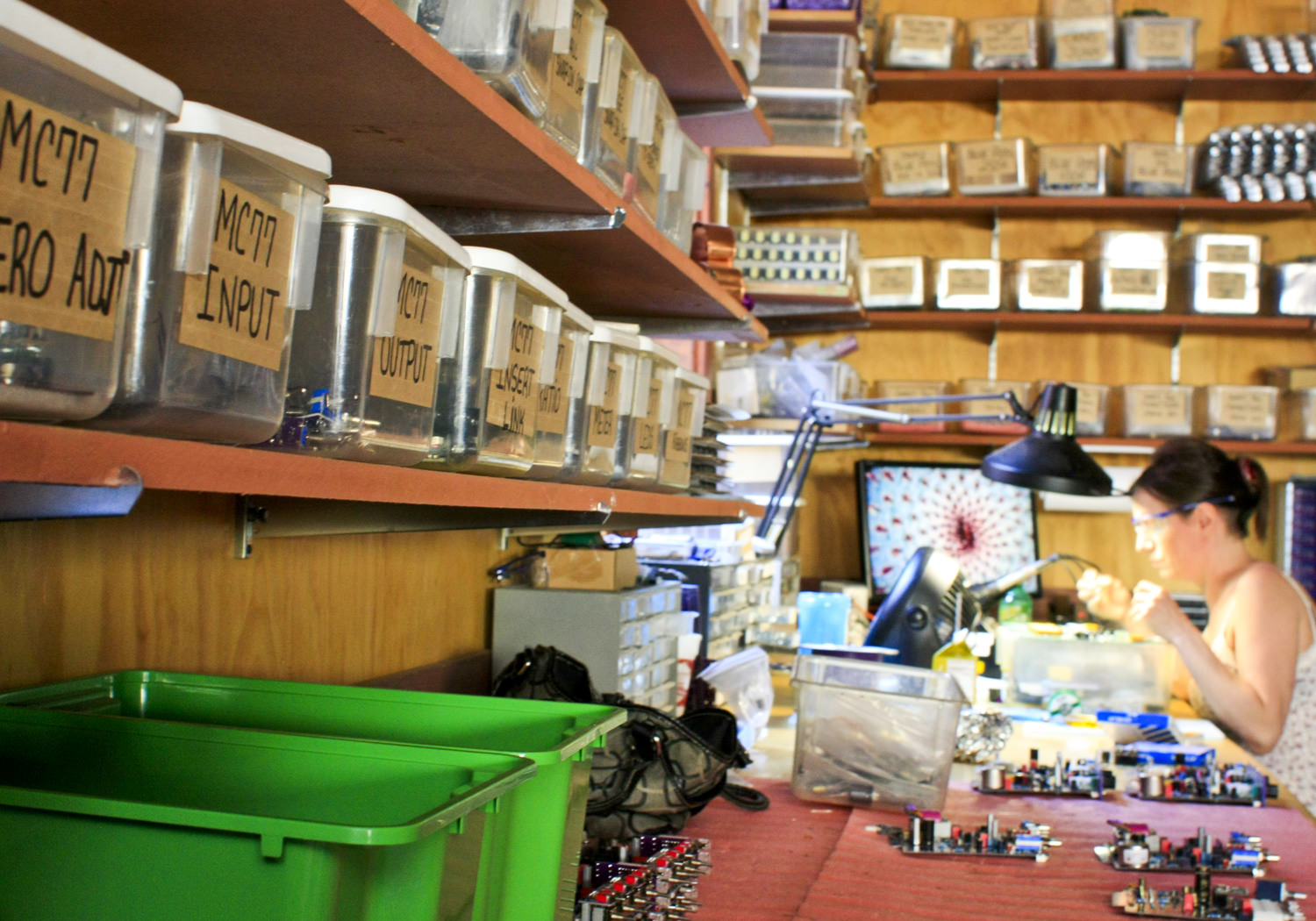
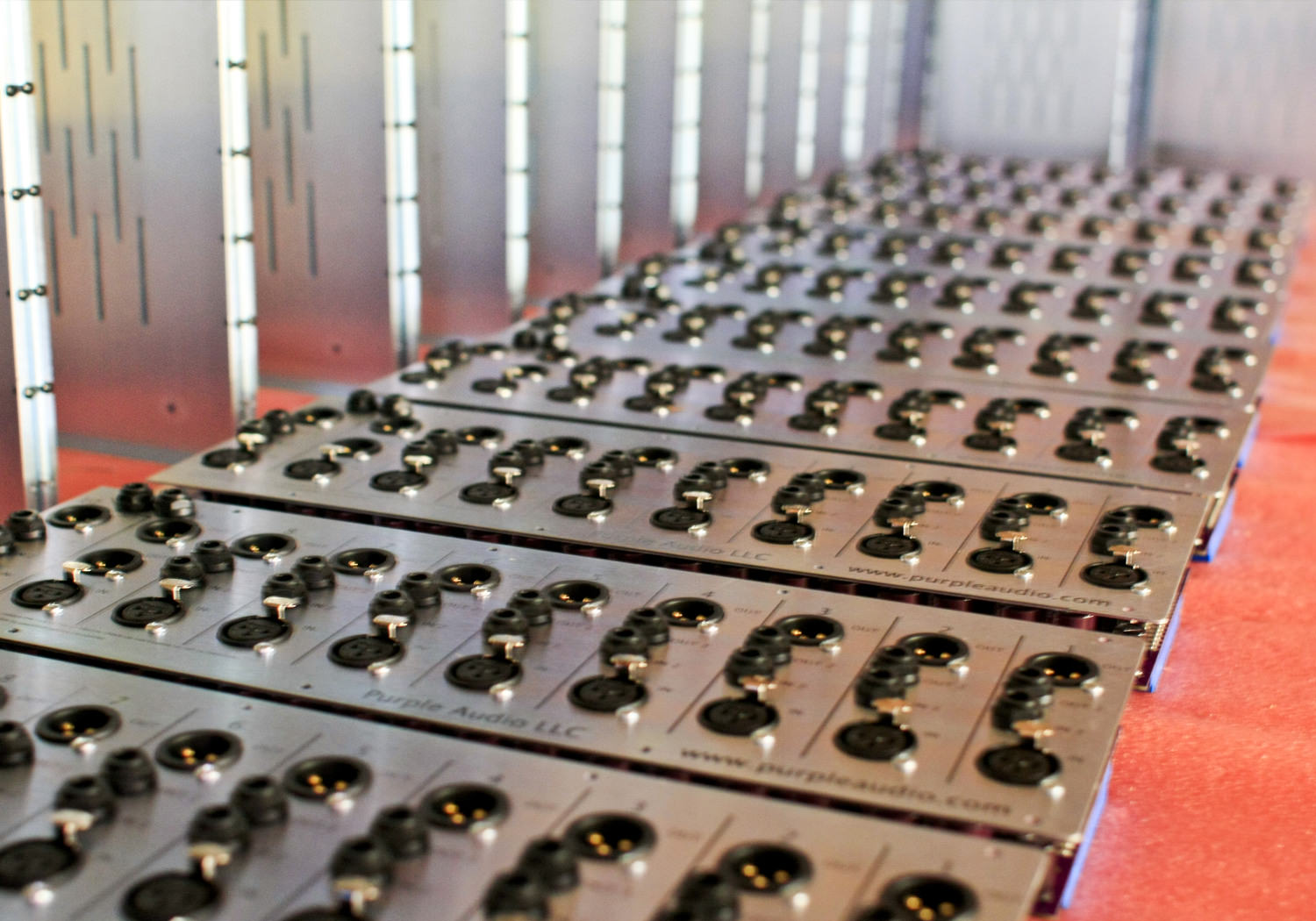
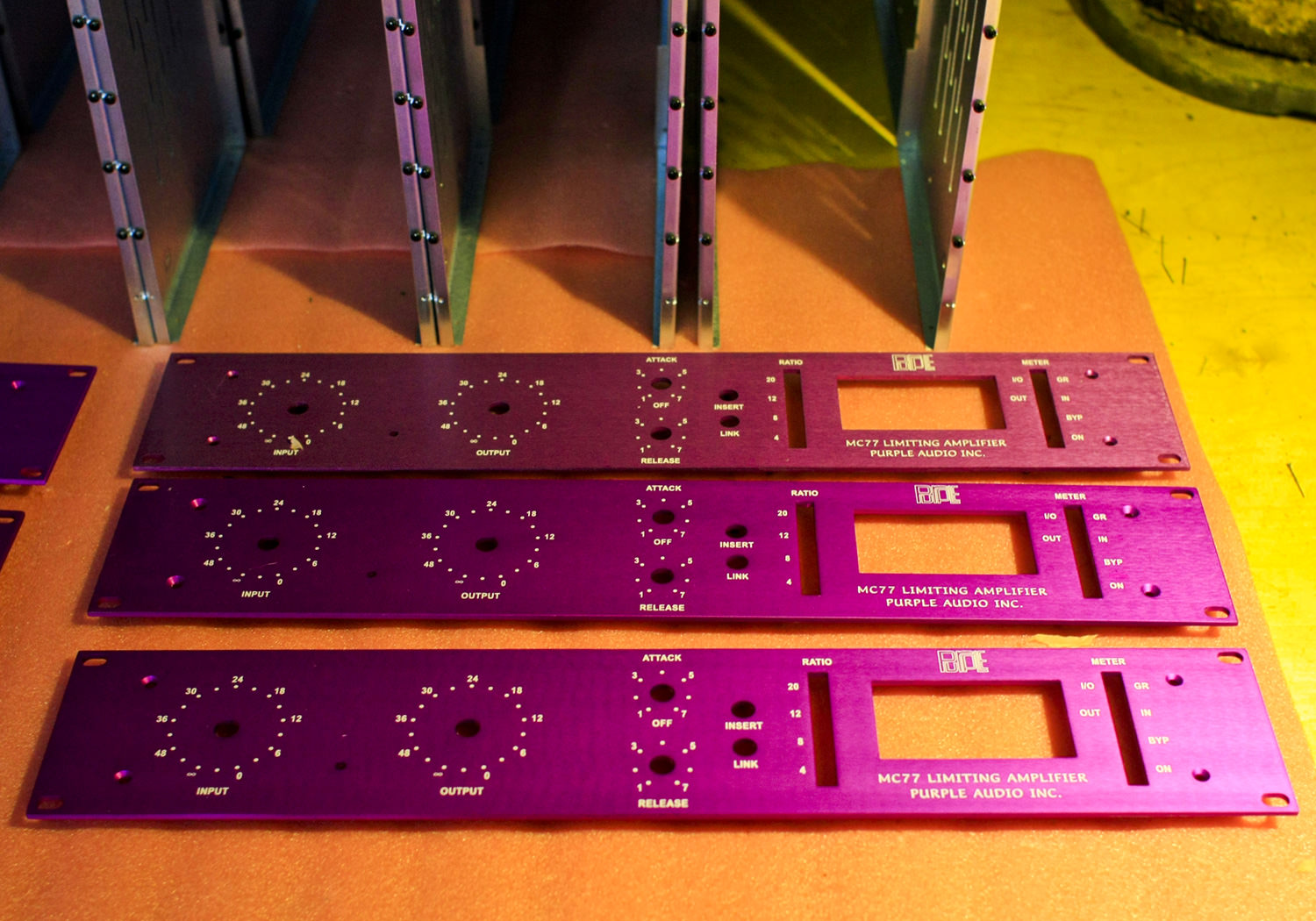
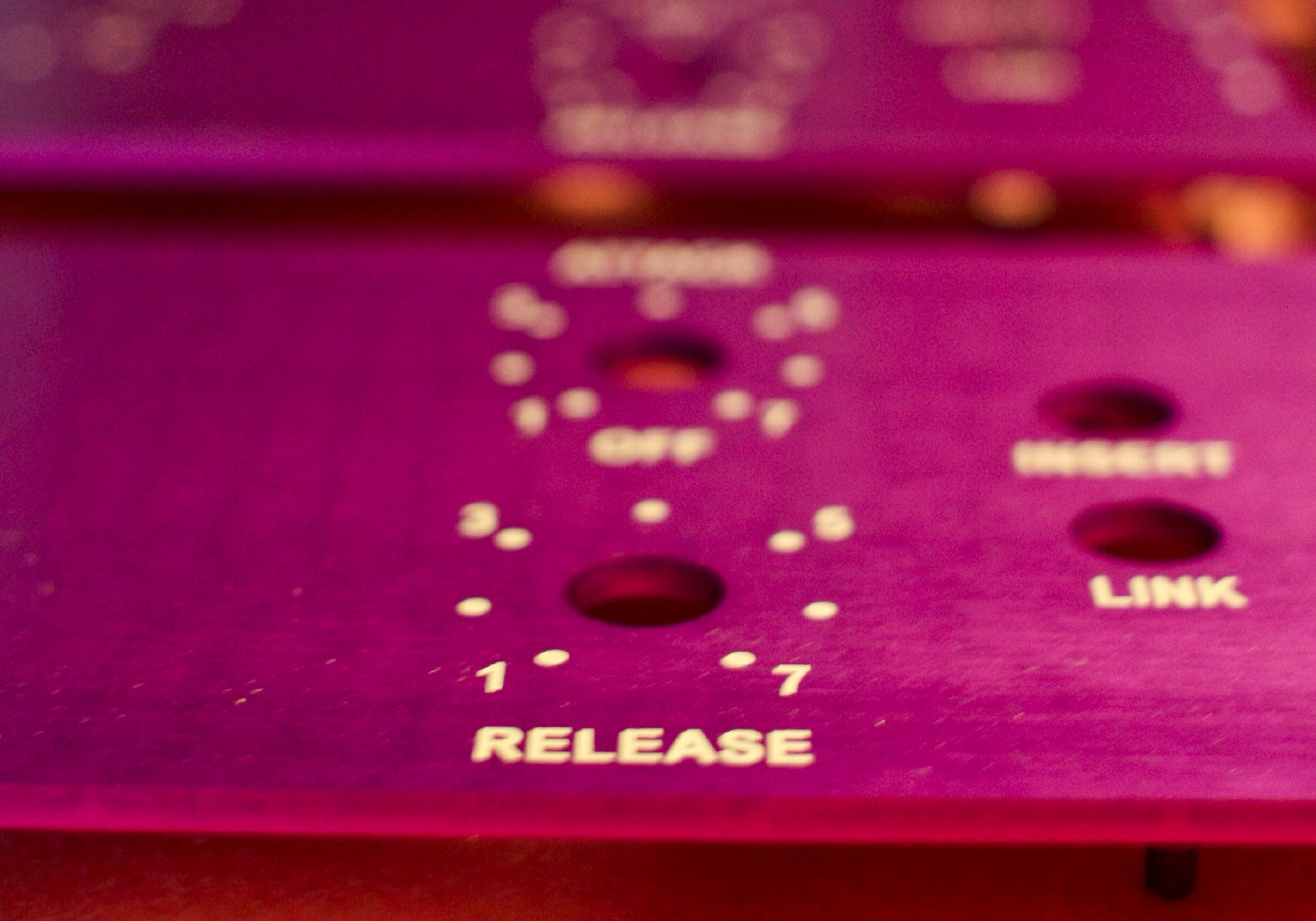
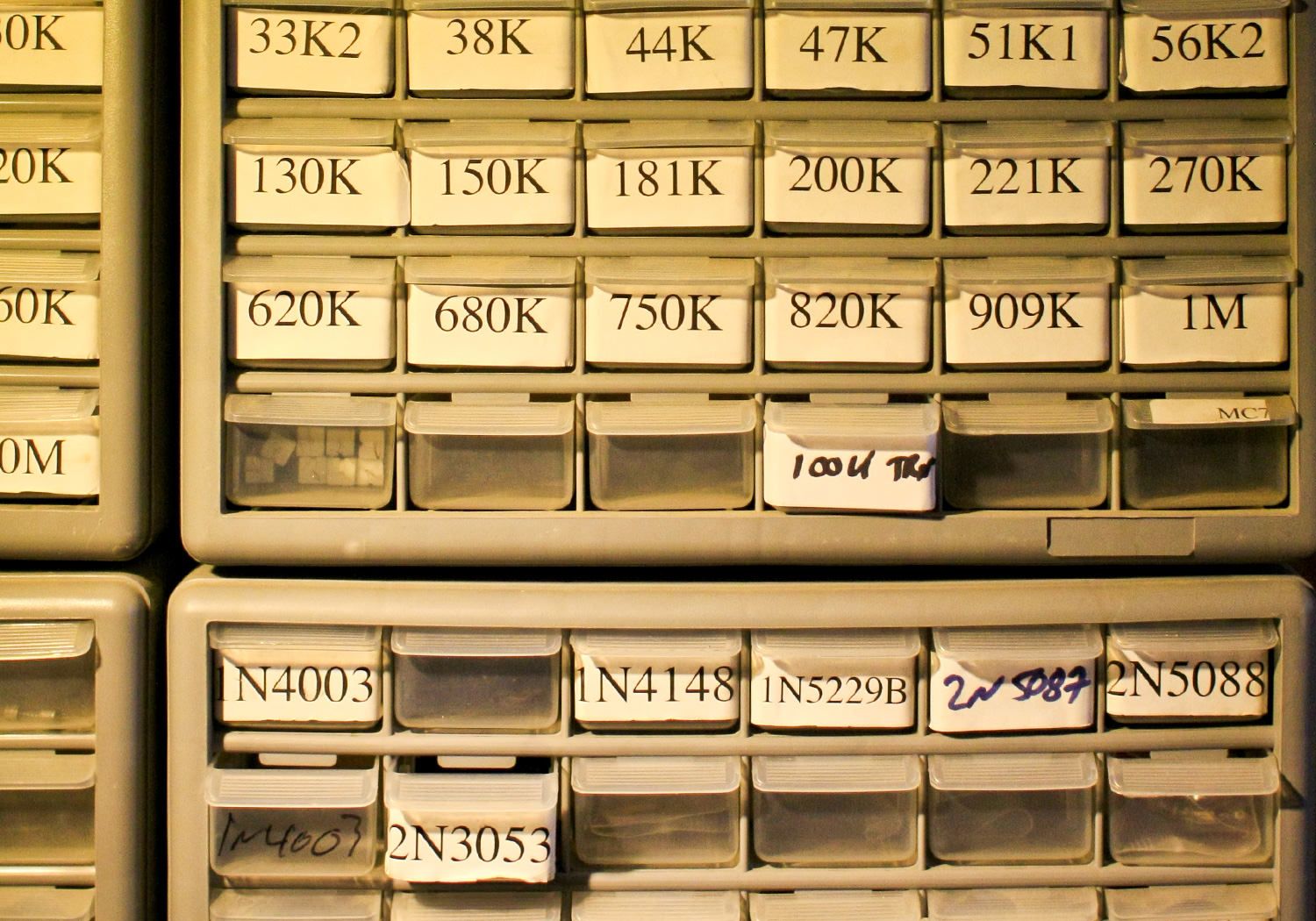
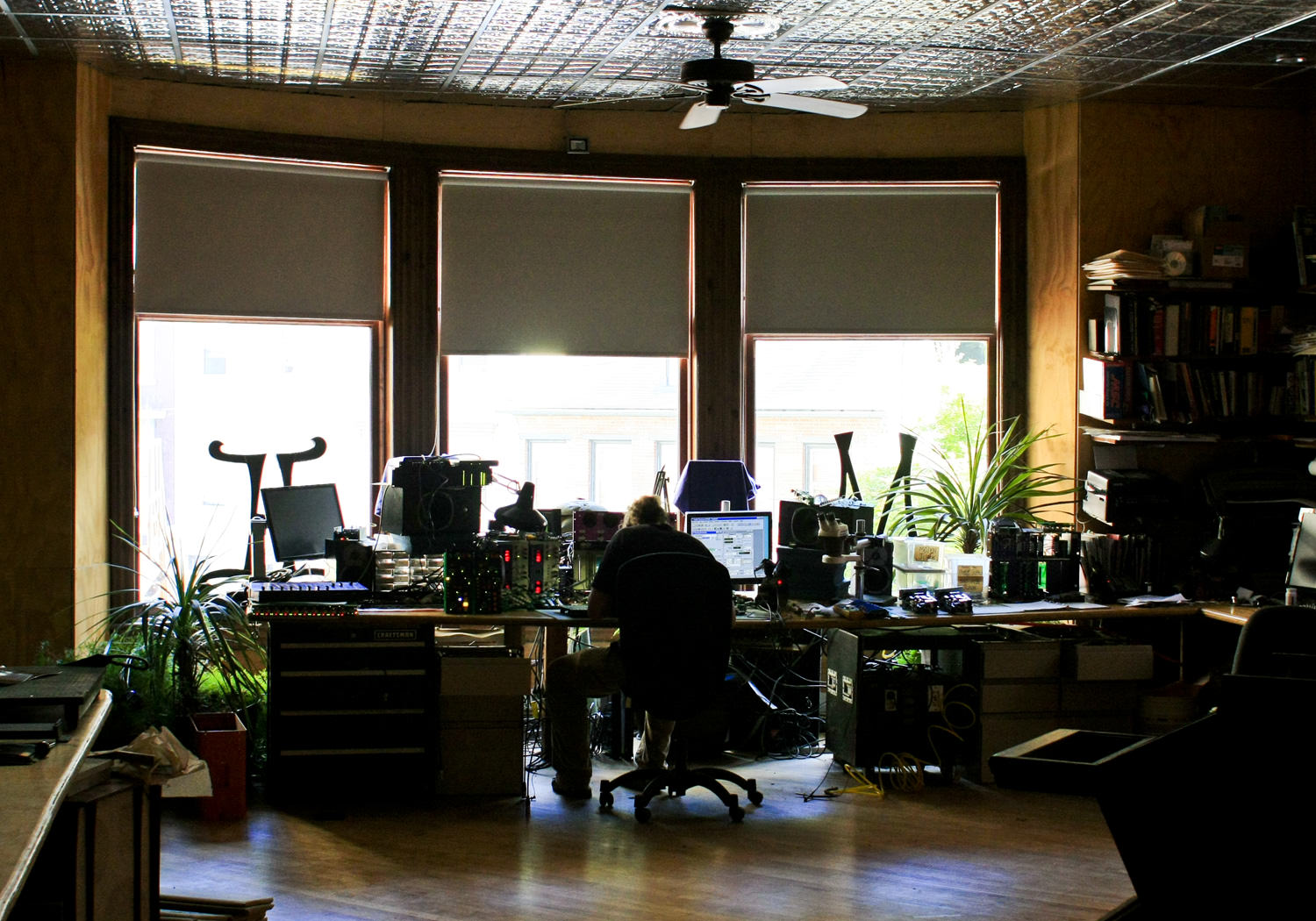
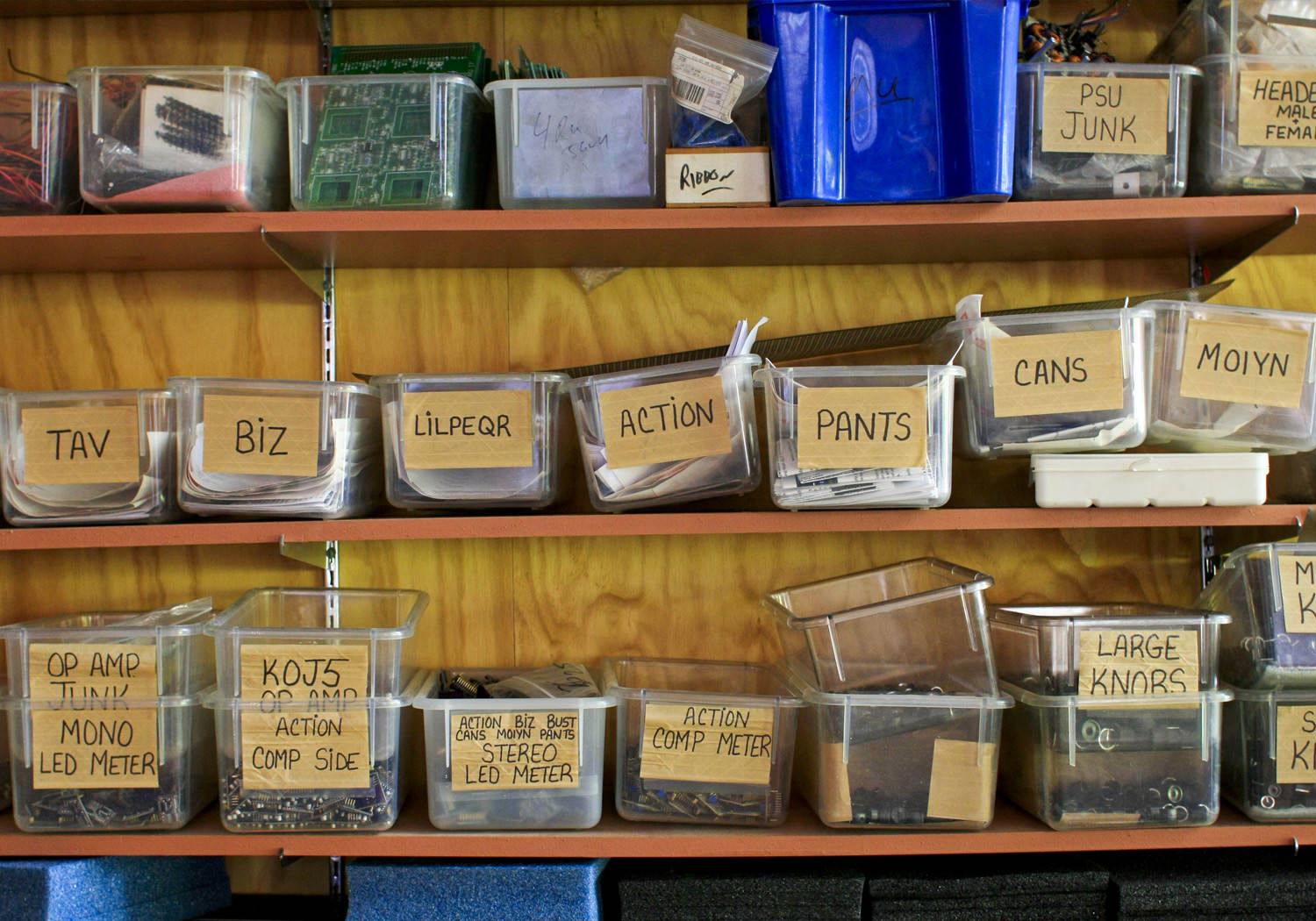
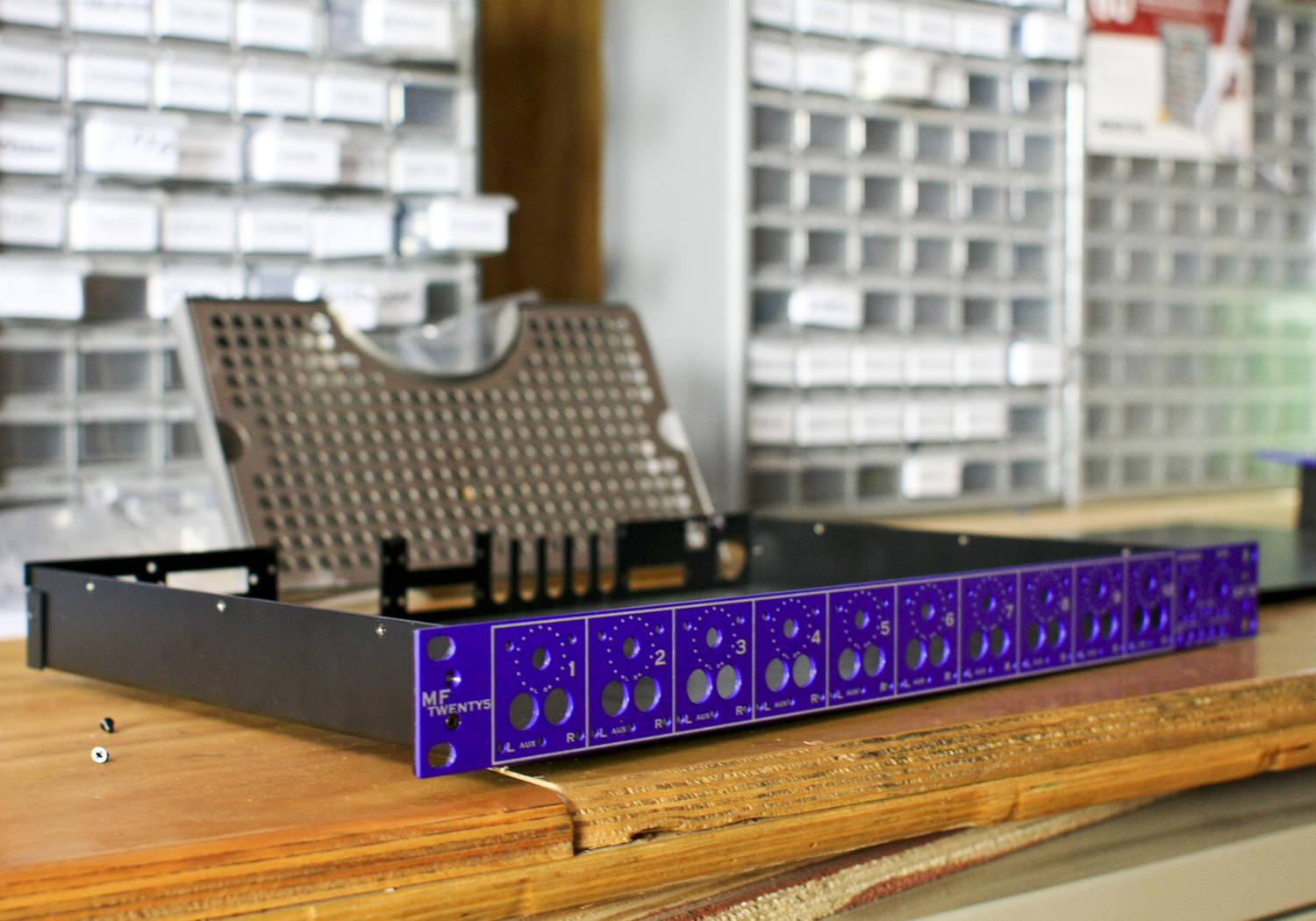

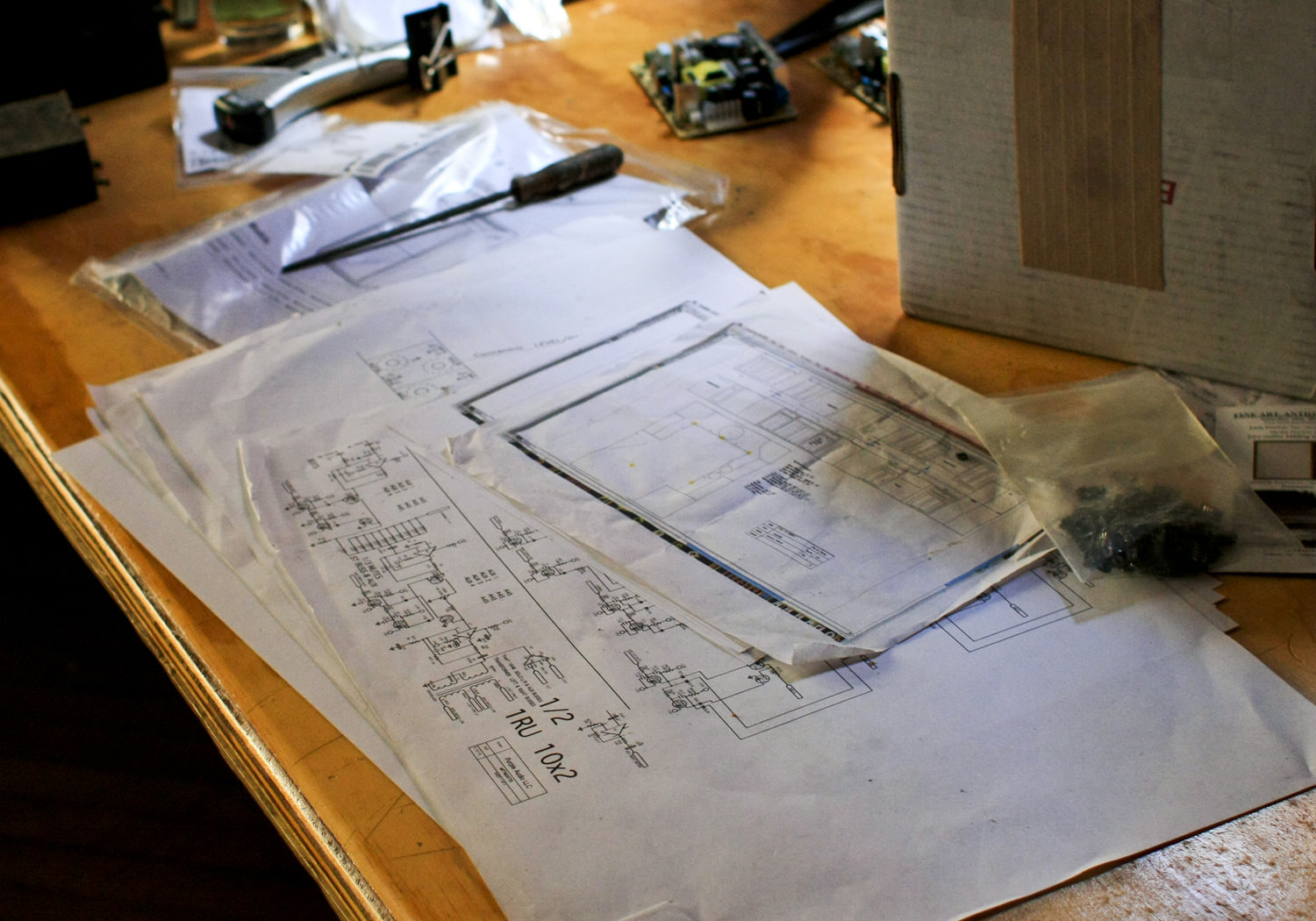
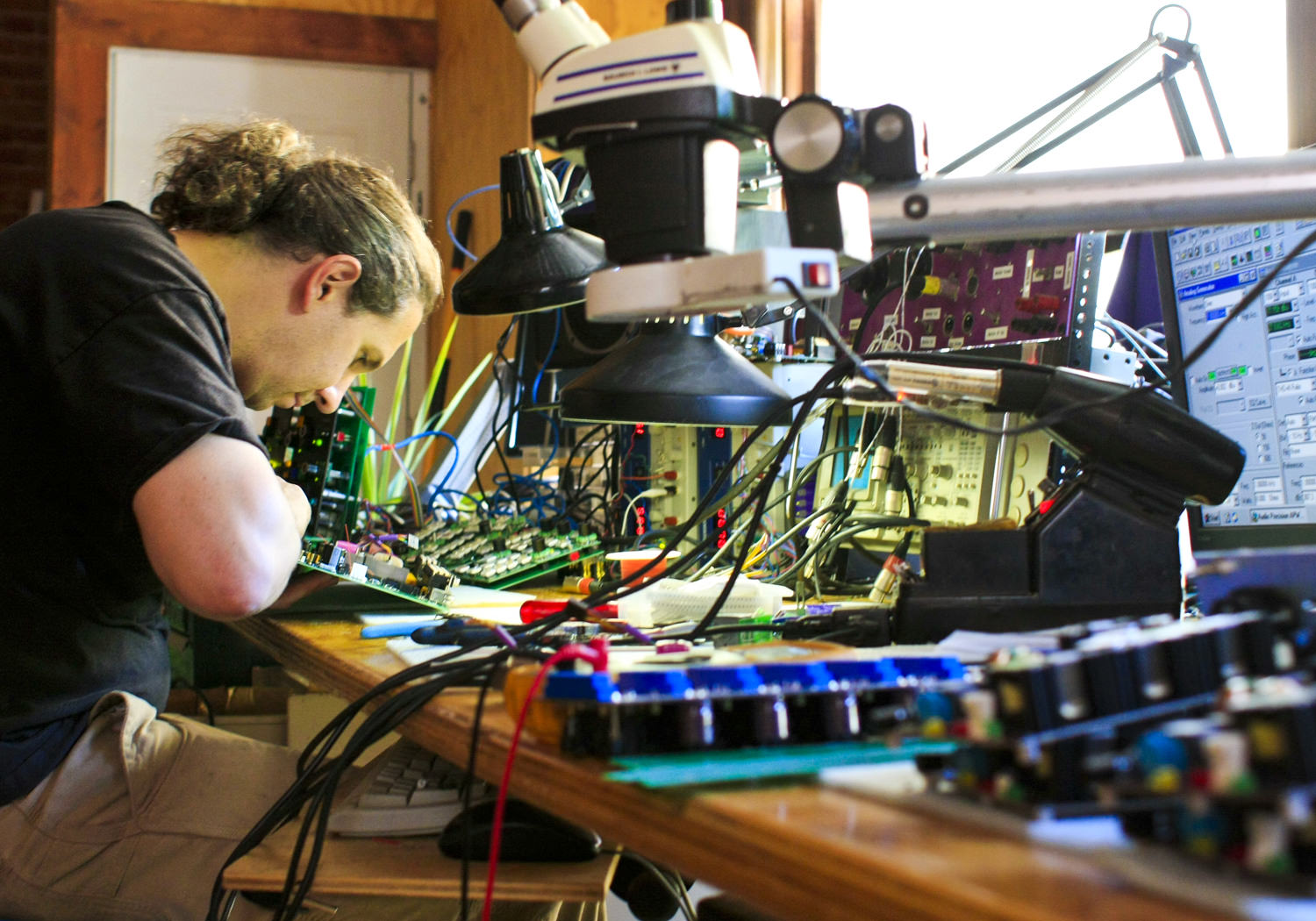
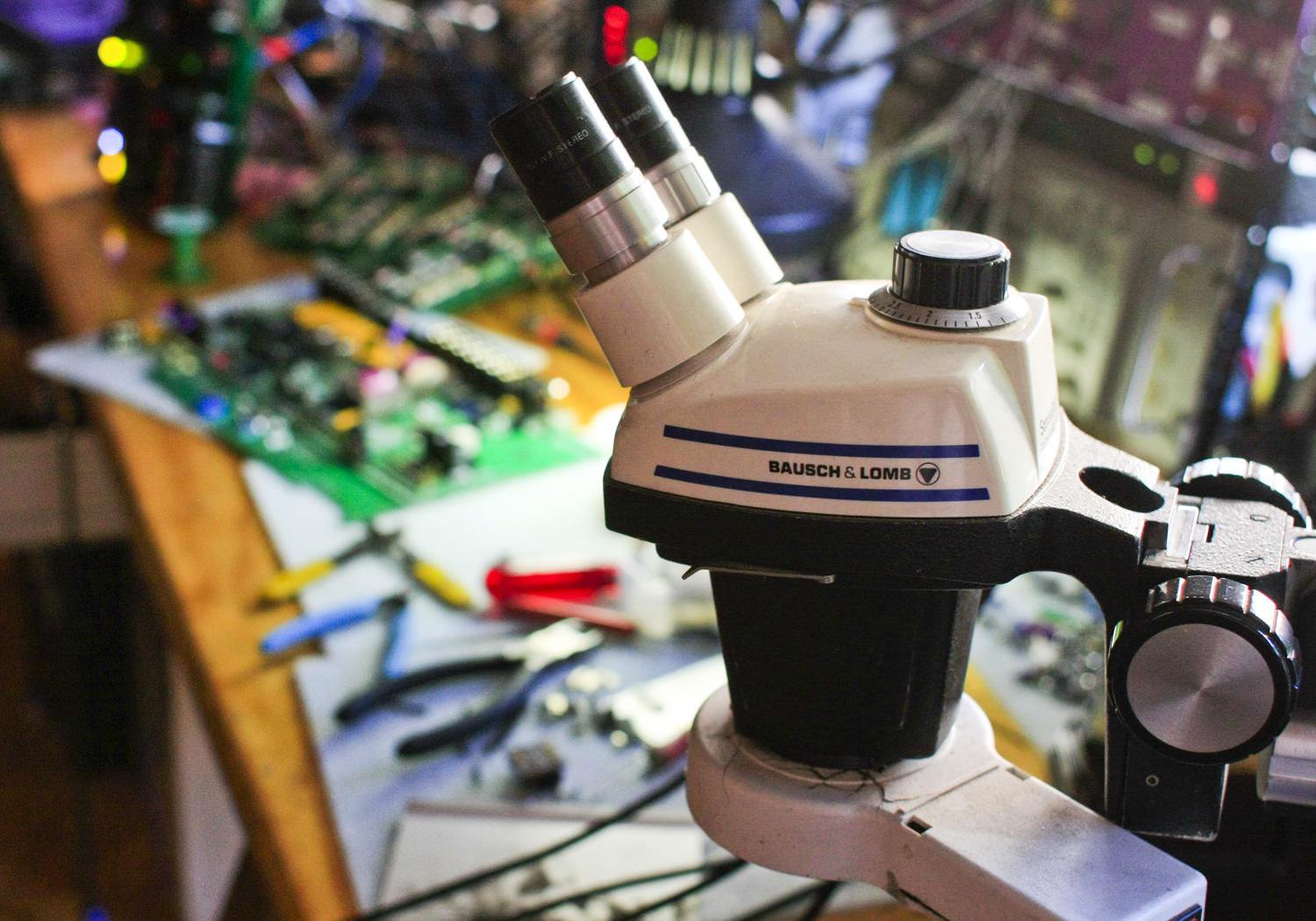
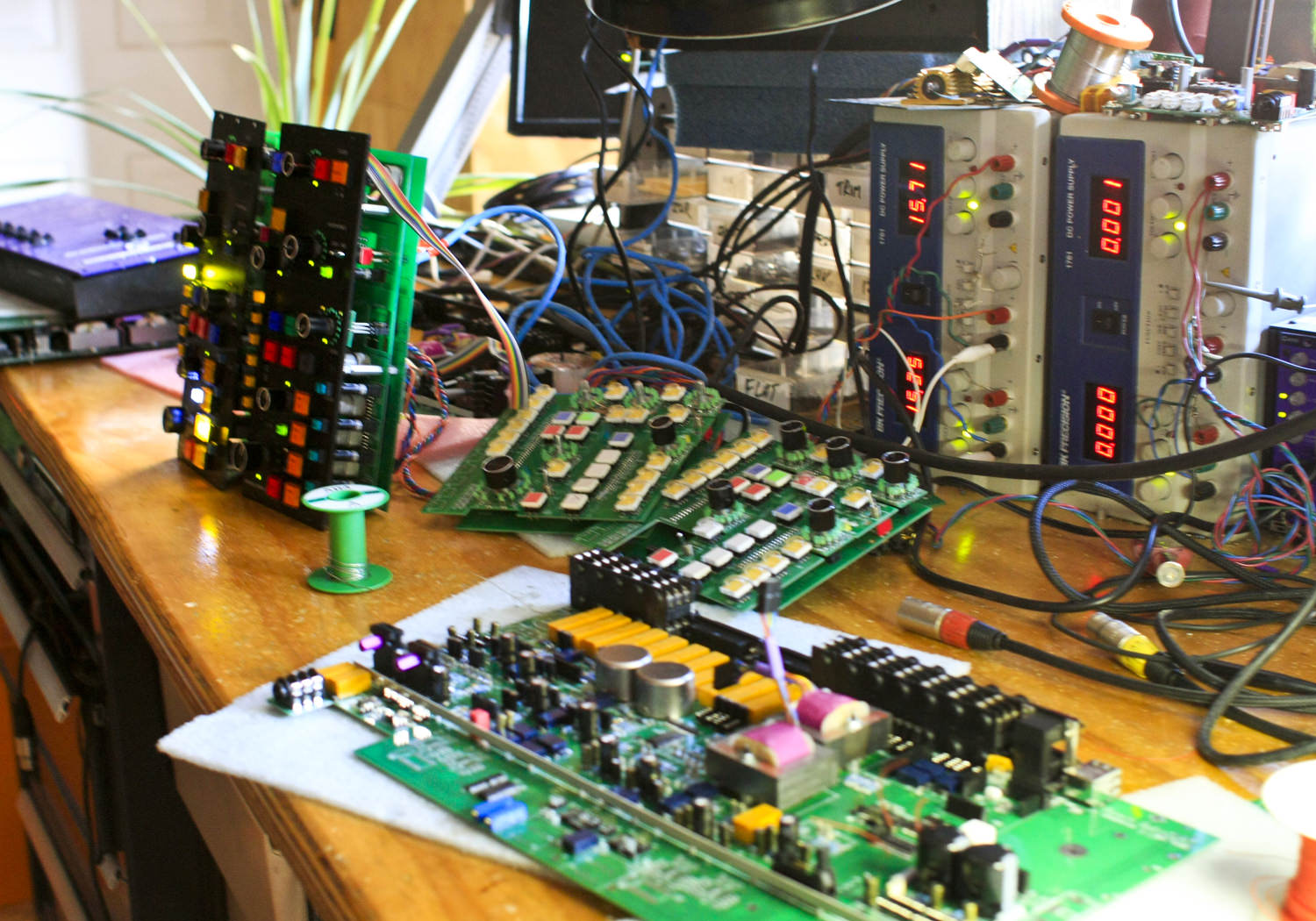
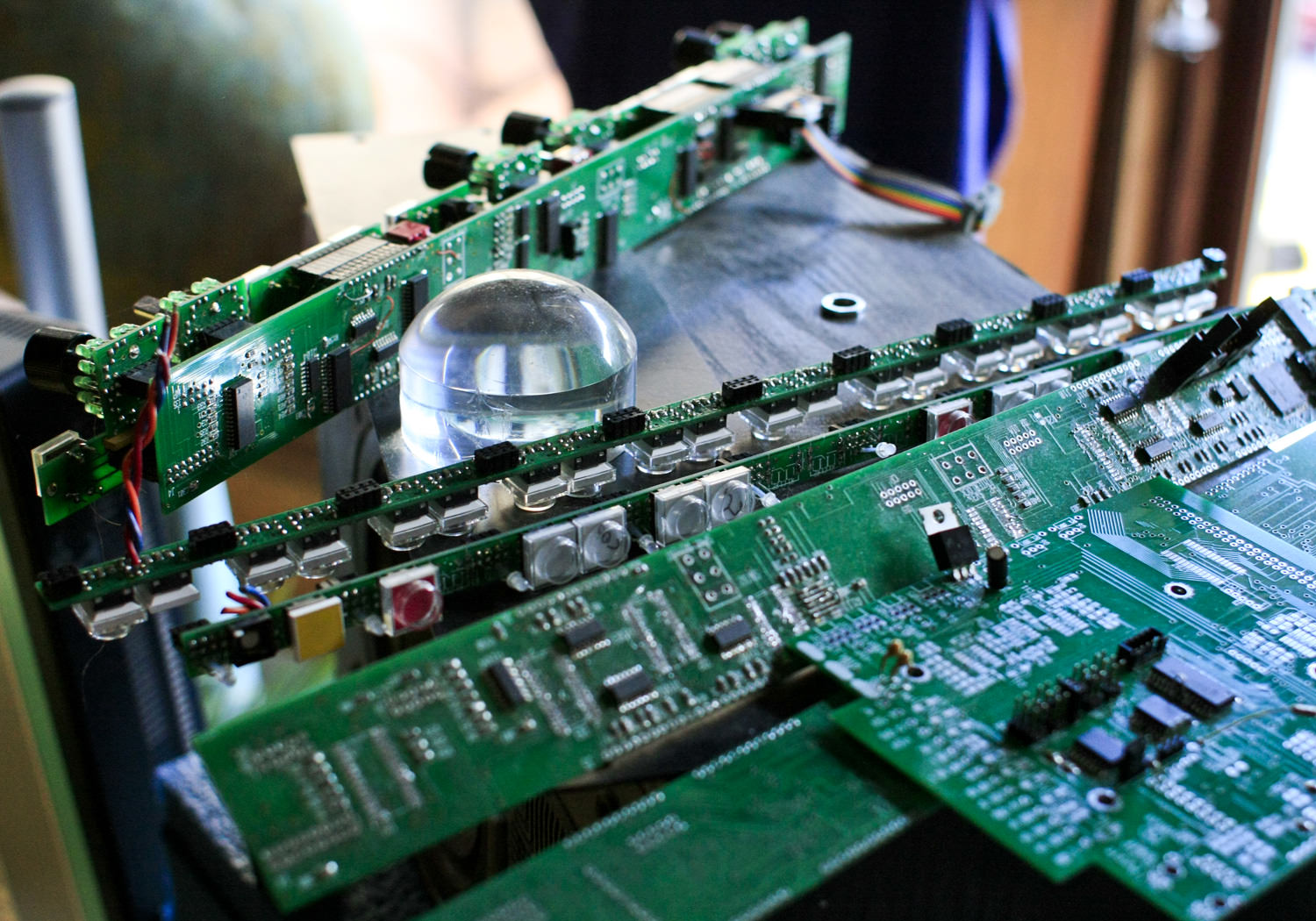
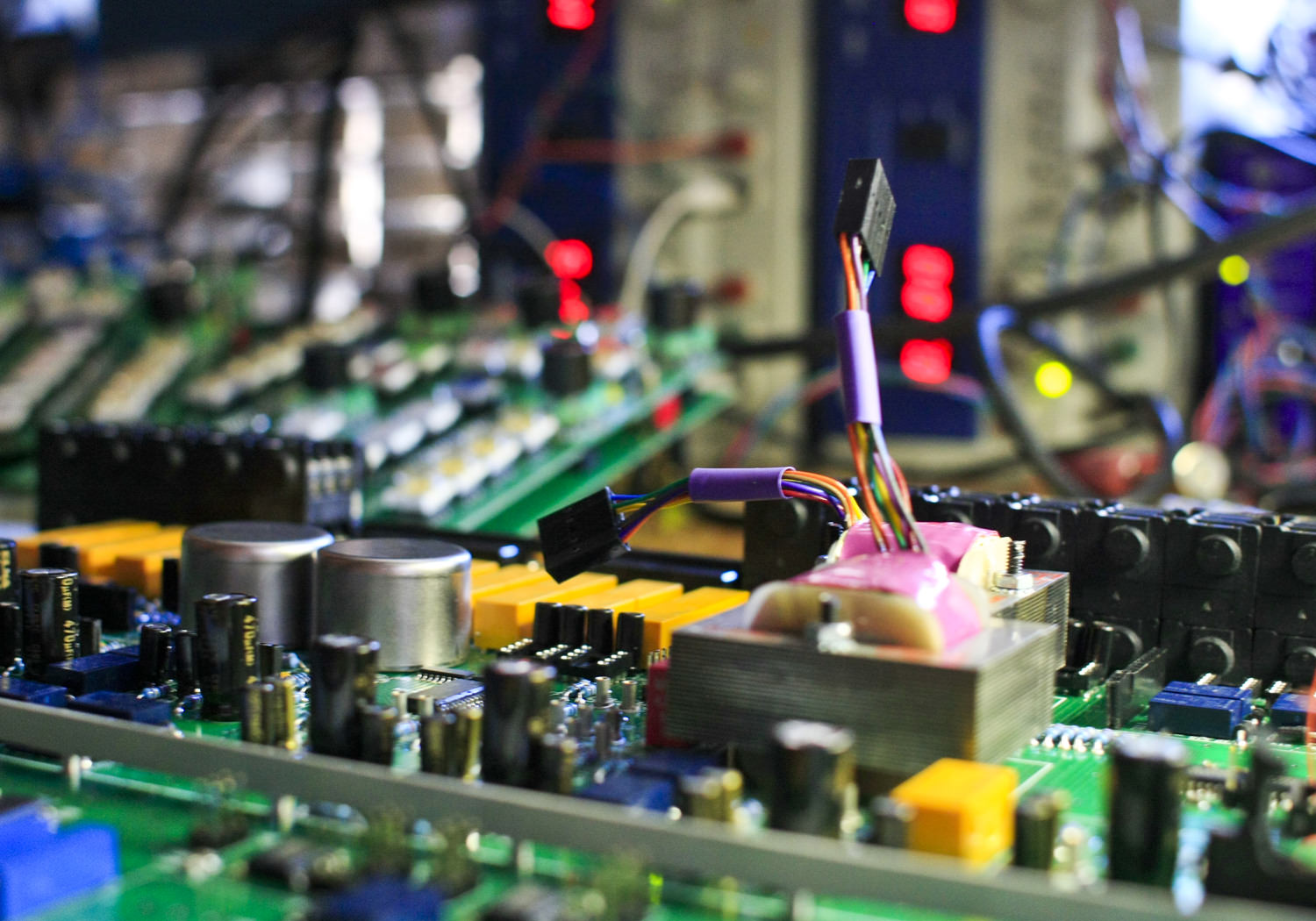
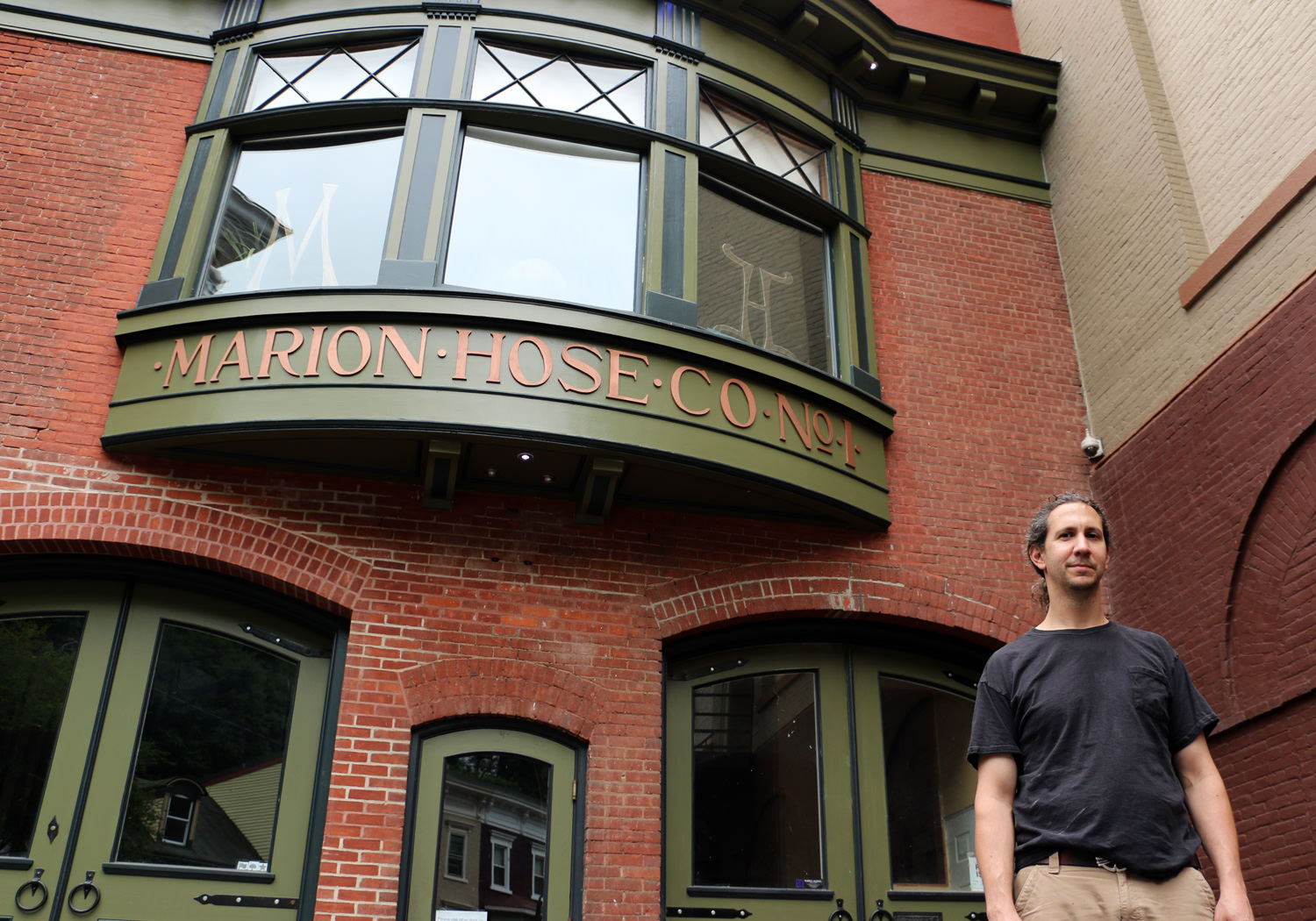
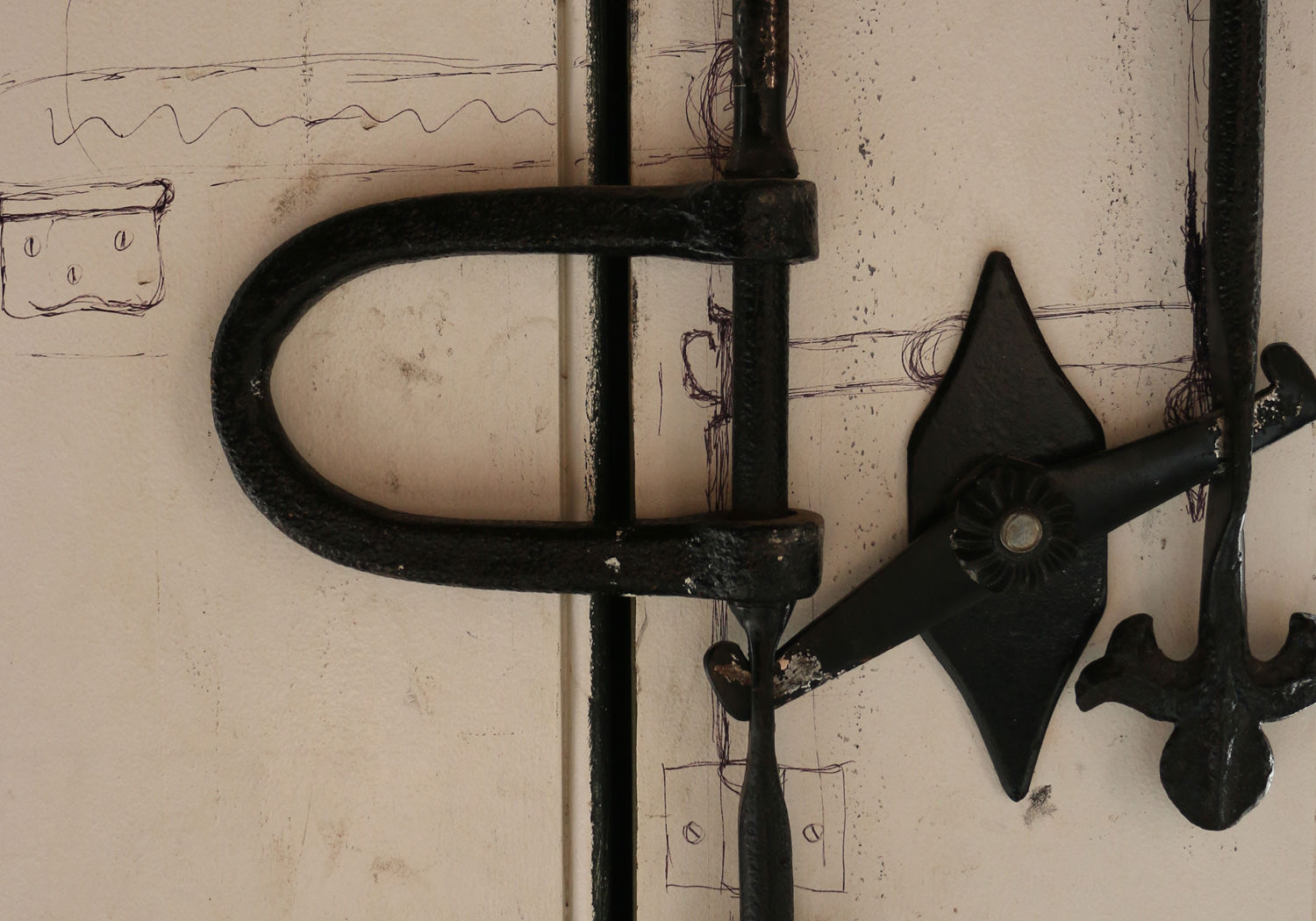
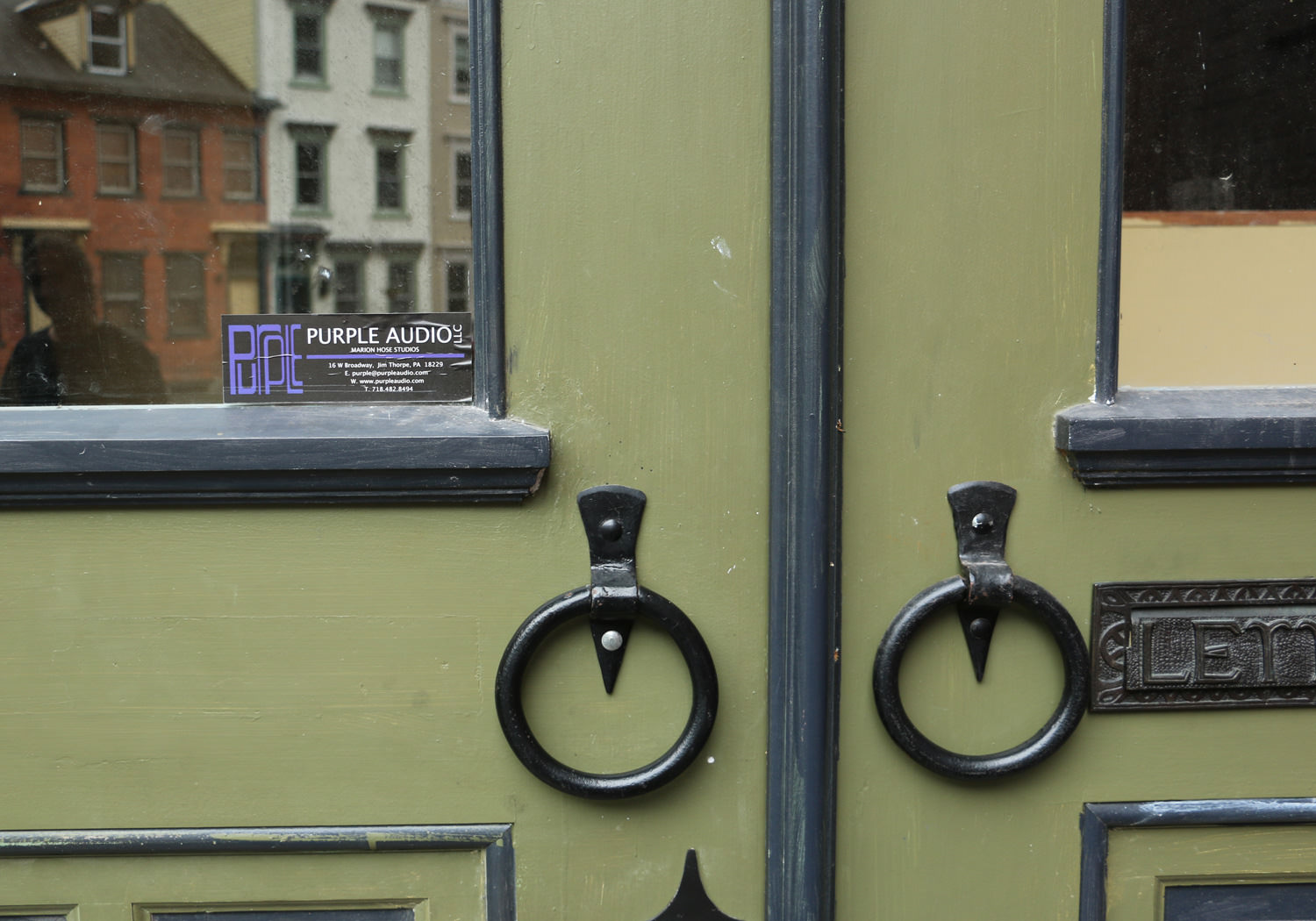
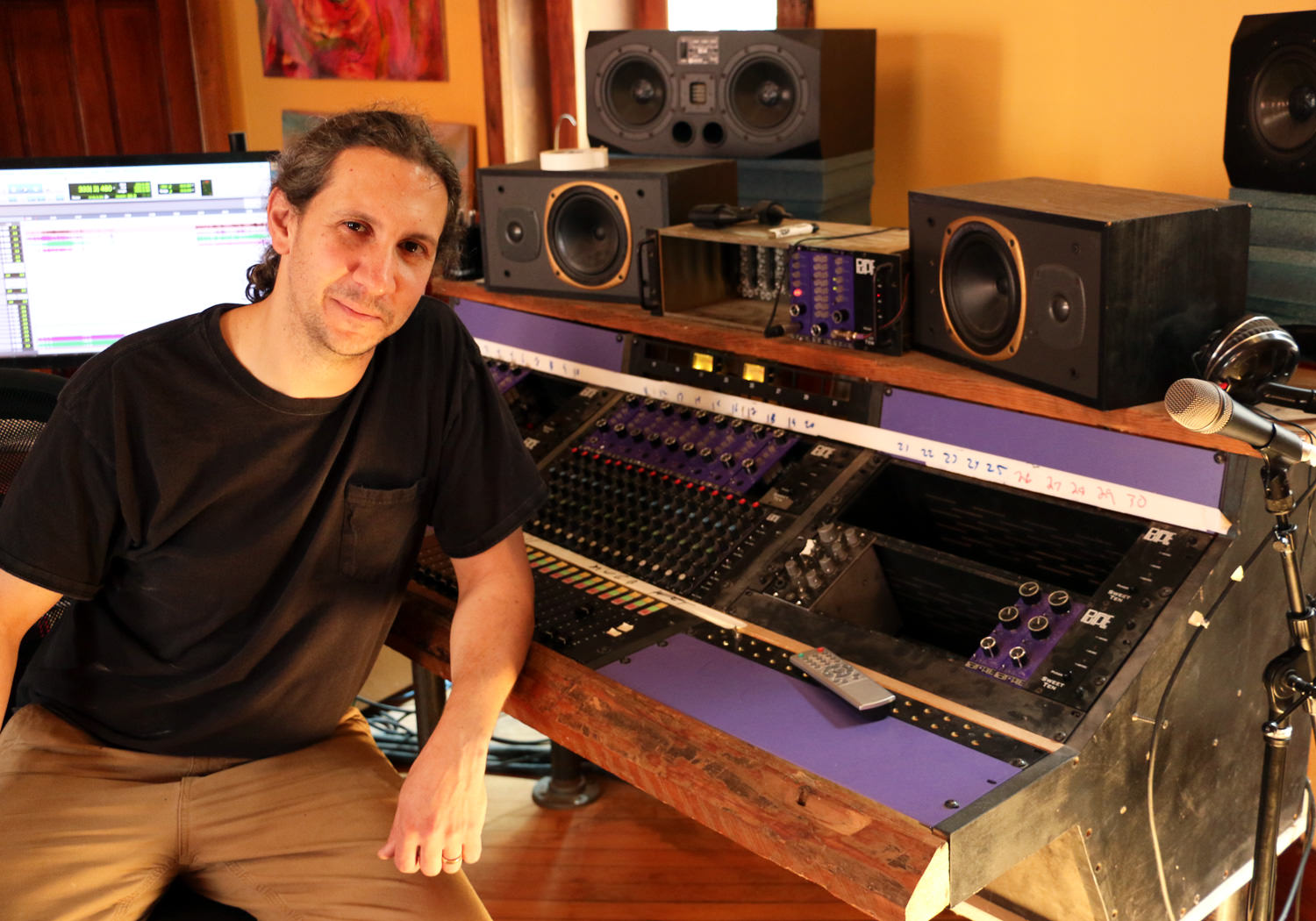