How did you end up in this field?
A friend of mine, who I'd gone to school with, Steve Desper, had become the mixing engineer for the Beach Boys. He told me I should move to California and get my foot in the door of the audio business in Hollywood. It turned out that the Beach Boys had all their touring equipment built by Quad/Eight. I managed to get a consulting job after building a few pieces of custom gear for the Beach Boys. Steve arranged for me to interview at Quad/Eight, and who interviews me but Deane Jensen! He was ready to launch the transformer company — this was in 1971. He was making noises about leaving his job at Quad/Eight, because he was a system engineer and he'd just become VP of engineering. The discussion turned over to the fact that he was working on this new amplifier — a really good audio op amp — because Bud Bennett, the owner of Quad/Eight, was such a cheapskate that he wouldn't spend money on an extra transistor for the amplifiers in the Quad/Eight gear. Of course that was the beginning of his work on his 990 op amp. We started talking about slew rates and all. At the end of the interview, Deane told Bud that I was really sharp and they ought to hire me. They did, then Deane went off and started Jensen Transformers. We really didn't see that much of each other, except at the occasional AES meeting, or something. I worked at Quad/Eight for three years. One weekend, frankly, I got stoned, and I came up with this idea for Compumix. We could gather a little data from the faders and a few switches. I'd learned from telemetry work I did before on how to generate digital codes, bi-phase especially, which I thought was particularly suitable for tape recording, since it's not polarity sensitive. I made this proposal to Bud Bennett, and much to my surprise, he thought it was a good idea. I don't know how much you know about Compumix,but it was actually very successful.
Was that the one that would rewrite mix data to another track, and you'd bounce back and forth?
Yeah, that's how the original worked. It laid down the initial data on one track, and then as you did updates it would bounce the data back and forth between two tracks.
People have to understand that this is long before SMPTE timecode was lurking around.
When I explain this, people say, "But that's so simple." But think about those days! There was no such thing as a floppy disk. The densest form of logic that you could get was standard TTL [Transistor-Transistor Logic], a few flip-flops, and NAND [Negated AND logic] gates in packages. This was all built out of very small-scale integrated circuits. A lot of it was very, very analog. It's not as simple as you might think, looking back. We established some industry standards, like using the -15 dB mark on the fader as a reference point for updating. That was my idea, which apparently caught on through the whole industry. We got it to market. We affectionately called the control unit the "ironing board," because it somewhat resembled that; and the processor was called the "mailbox." The mailbox had all the VCA control channels, decoding hardware, and line amps in it. Much to my shock, Bud actually gave me a rather large bonus that year for Compumix, because it was such a financial success.
What jobs did you have after Quad/Eight?
I got lured away. A guy walked through the front door of Quad/Eight and said, "Who designed Compumix?" They showed him to my office, and he just kept making higher and higher offers. It was this start-up company called Laserium that did laser light shows. They were looking for a way to automate a laser light show. I moved over there, and I must have almost doubled my salary. I was over there for seven years. Actually, in '76, I filed a patent for a digital recorder based on a VHS machine. It used the mechanics, but completely gutted the electronics. We could record four channels of audio, as well as all the control information for a laser light show on a videocassette. It was a very popular show, but the company got mismanaged. Capitol Records was looking for somebody; I went out there for an interview, and I got a job there as manager of electronic development and engineering. My major job was to completely overhaul all of the high-speed tape duplicator electronics for the XDR cassette tape program [eXtended Dynamic Range]. One of the engineers that worked under me, Keith Thomas, and I sat around one day and brainstormed about a digital loop bin. We had digital masters for all the music, so why did we need to make this intermediate analog running master, which was nothing but trouble? It was a 2-inch tape running at 480 inches per second — this machine made you hold your breath whenever you turned it on. Why didn't we just get a large memory at high speed, load all this music in there, and then play it back at 64x speed into some D/A converters so that the pancake reels on the cassette tape would be first generation analog? We ended up having to design our own DACs [Digital-to-Analog Converter].
You're printing to the cassette at a really high cassette speed.
At 64x actual speed.
So your digital frequency has to be very high.
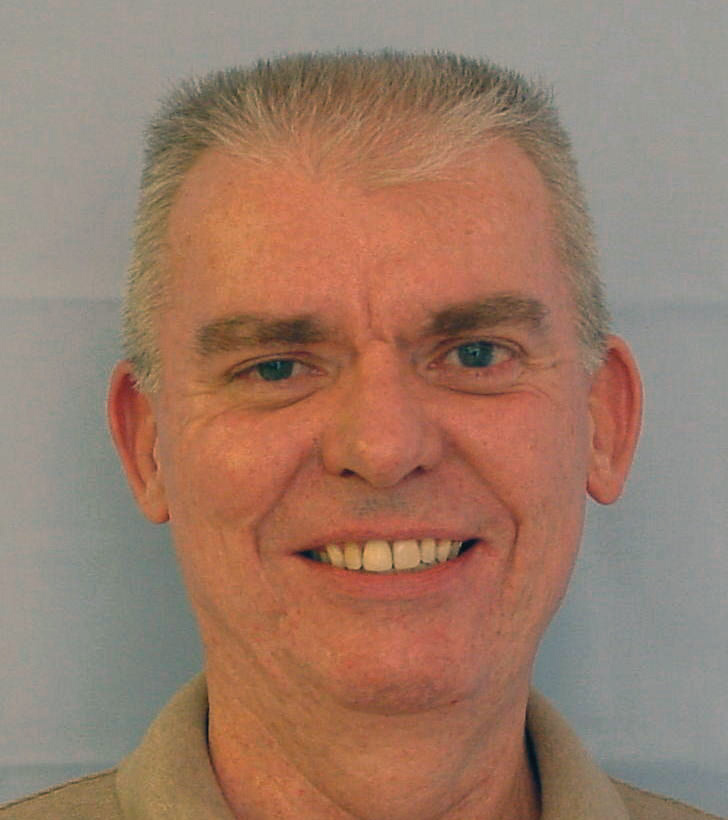
The analogue signal at 20 kHz now became 1.28 MHz. While I was there, I also implemented Dolby HX Pro on the production line for all the cassettes. We didn't like the Dolby implementation of it, so we rolled our own. That's what I get for being an analog circuit designer... it's never good enough. For over a year I'd been putting in 70 to 75 hour weeks, working around the clock. We were always behind schedule on this project, but the boss sent me on a vacation. When I came back, they had returned all the gear, canceled the project, and they'd done it all while I was gone. I was outta there.
And then what?
My friend, Steve Desper, who I mentioned earlier, had discovered this amazing patch using filters and equalizers on mixing boards. It had this amazing stereo enhancement effect that widened the stereo image and made it sound like there were sources in the room that were way beyond the speakers. It eventually was called Spatializer. He wanted me to build a professional version of this that would work with multitrack playback. Of course it had to have transformers, so we went out to Deane's office to talk about which transformers to use. I told him that I'd just quit my job at Capitol Records. His eyes lit up, and he asked if I'd like to work with him doing consulting. He got so bored sometimes at the transformer company; he really liked taking on other peoples' projects and using the software that he'd developed to solve these problems. I said, "Sure. Why not?" We set up an office in my house in Sherman Oaks. He'd come over in the evening, and every weekend we'd spend at my house in the lab. He had tons of projects. People would ask for these impossible filters. We brainstormed a lot about the 990 [op amp] as well. We did that for about a year and a half. He never wanted to talk much about what was going on at Jensen, so I didn't find much out about the actual business until after his death.
How did you end up running Jensen Transformers?
Deane left it to me. There were lawsuits that took years to settle. That was really the dark side of Jensen. For about the first four years, I wondered if I was throwing good money after bad. I had to re-mortgage my house, and I was borrowing money from everybody I knew just to make payroll and keep the doors open. It was against the advice of my lawyer and the company accountants, who both said that I should close the doors and walk away from the mess. I felt like I owed Deane a lot more than that. He worked a long time to get his reputation, and I didn't just want to see it go down the drain. But we did turn things around. About 1994 or 95, we started to operate in the black. The lawsuits were all settled, and we introduced the ISO-MAX product line, which is part of what saved us. By then, the Pro Spatializer was also in full production by Spatializer Audio Labs, and I was getting quite a substantial revenue stream from that, which I was plowing into Jensen to keep it growing.
What is the ISO-MAX product line?
One of the guys I met while I worked at Capitol Records competed in these dB drags, where you see how loud you could get your car stereo to go. He always installed a Jensen transformer in his systems to get rid of all the ground loop issues, like the alternator whine and the turn signal clicks and pops. He came to me one day and said, "There are a lot of people who would buy these transformers, but they don't know which end of a soldering iron to hold." He told me that I needed to put them in a box with connectors. We tried that on the car stereo market, but people said, "I'm not going to spend this much on this box." But then somebody told us about this new trade show called CEDIA [Audio Video Technology Tradeshow] about home theater. We went to that show, set up a booth, and those things started flying like hotcakes. All I had to do was mention ground loops to home theater people, and they suddenly became interested.
Jensen has always stood for quality. You see legendary brands like Altec Lansing at this point used for branding cheap speakers.
That makes me cringe, the thought of something like that. I've always tried to represent the company as the smartest company around, when it comes to transformers. When I first took over the company in 1989, I had used transformers to solve problems, but I couldn't really explain to anybody why they solved problems better than any other solution. That led to my AES paper in 1995, "Balanced Lines in Audio: Fact, Fiction, and Transformers." It turned out to be an earth-shaking paper.
What would be a simple way to explain that to our readers?
You've probably heard the most common, but wrong, definition of what a balanced interface is. The standard definition goes something like, "There's the plus and the minus line. The plus has a signal on it, and the minus has a mirror image of that signal; equal and opposite in polarity." That's absolutely wrong. A balanced interface is defined solely by the impedances of those two lines, with respect to ground. In an unbalanced interface, one of those two wires is grounded, so the other one that carries the signal has a higher impedance, something above zero, which is determined by the source and the load. In a balanced interface, what makes it balanced and gives it all its magical noise-rejection properties, is that the impedance, with respect to ground, of those two lines is equal. It doesn't mater where the signal is at all. You can put all the signal on one of those lines, the other, or split it up between them, as is popularly done. But it's not required, and it has nothing to do with the noise rejection. The problem with using a single op amp and four resistors [in place of a transformer] is that its common-mode impedances are really low; a thousand times lower than a transformer. This means that this bridge can be unbalanced by even a fraction of an ohm from the connected source. That's why, with so much gear today, how much noise rejection you actually get depends exquisitely on the source and how balanced it is. It's my message: Transformers are fundamentally different, and far superior, as a balanced-line receiver. I'm a born skeptic; I'm always looking for the non-obvious answers and sometimes I find them.
Peter Janis was saying that he's rearranging the company, as far as efficiency.
We never had a lot of surplus cash. But right away Peter bought two, brand-new, Meteor computer-controlled Swiss-made winding machines. I think that brings us up to a total of seven or eight machines. He hired the staff to run those. Our accounting department has always been a total thorn in my side; he also got that straightened out right away. I know there are ways to save money, but if it'll cut into the quality and performance of the part, I'm not interested. However, if there are ways to reduce the labor and/or improve the uniformity, and also reduce costs, yeah, I'd be very interested in that. I've never pretended to be a great business manager. I ended up as owner and manager of Jensen by default. My training has always been as an analog circuit designer, and that's all I really love doing. When we started not being able to deliver his parts as fast as Peter wanted, he started making noises about, "When are you going to sell this company, Bill? Aren't you going to retire some day?" The hints started getting heavier and heavier. Last year, it got down to the point where I told him, "I'm almost 70 years old, and I'm really not enjoying all this management stuff." At that point we had about 15 or 16 people on the staff. I'd never managed that many people before, and it's not easy. On my 70th birthday, April 14th of this year, we signed the final deal, and Jensen became owned by Radial. He has promised me that he will keep it independent, separately managed, and, that as much as he possibly can, he'll uphold the standards that we've held over the years.