How did you begin with engineering?
I've been in music my whole life. I was studying piano at age 4. My mother got me piano lessons because I'd hear a song I liked, and then I'd sit down at the piano and start trying to pick out the melodies. I would play with both hands, so I began studying classical piano. When I got to high school age, I was playing in garage bands, doing keyboards, background vocals, and some lead vocals from time to time. As I got into college, and we started doing demo tapes, I never liked the way that they sounded. They never came out of the speakers the way that I heard them in my head – especially the songs I wrote. I thought to myself, "I need to learn what that person sitting behind the console is doing." I had no clue what was going on when they were turning knobs. I understood that pushing the fader up made it louder and pulling it down made it softer. I began going to school for it at Georgia State University, but I was interning at a studio from day one, asking a ton of questions, and learning everything that I could. Pretty soon I was an assistant engineer and I worked my way up the ladder. It developed out of necessity – needing to record my own music.
What was the year of that first demo?
We started doing demos around 1987. In 1989 was when I began going to school and interning.
That was around the era of 4-track cassette recorders. Did you ever do any of that?
I was fortunate in that I went right into formal studios. I figured that if I wanted to do this that I wanted to learn from the best, so I walked into the best studio in Atlanta – which, at the time, was called Soundscape [Studios], and then became Bosstown Recording (owned by Bobby Brown) and is now Stankonia [Recording Studios], owned by OutKast. It was the best studio in town, where all the real records were being made. This was at a time when becoming a recording engineer was not as publicized or well-known as it is today. There was only one academic program in the state of Georgia for recording engineering, and that was at Georgia State University. Now you have all of those programs packed full of people, so you have a lot coming out every year competing for internships and work in studios. In the late 1980s that wasn't the case. I emptied garbage cans, swept the parking lot, vacuumed, and cleaned bathrooms; all of the things an intern is supposed to do. They were gracious enough that once they knew I had some grip on the equipment and I respected it, they would allow me to bring my own bands in during off-hours whenever there was nobody in there – usually between midnight and 6 a.m.
Yeah, I know that shift. [laughter]
That was a big growing experience for me because I made a lot mistakes with the recordings. But it was my own band, and we were having fun and creating.
What are the advantages and disadvantages of formal engineering training?
I got into my internship before any of my recording classes at Georgia State. This was in the infancy of academic recording programs. By the time I got to the actual hands-on recording classes at Georgia State, I knew more than the person teaching the classes. It's no knock on the professors; they were composers more than engineers and they happened to have the studio available – the facility was used as their classroom. They were very good composers, but they were often limited as engineers. I'd ask, "Teach us how to align this tape machine," or, "The different patterns for microphones." They'd say, "Uh, you don't really need to do that. Once the machine is set up, it takes a lot of work." It was clear the instructor didn't know how to align a tape machine. But, as an assistant engineer back then, aligning the tape machine was the very first thing you did the minute you walked in the door. You'd be setting up for a session and align the damn tape machine. You might have to check it a few times throughout the day. I learned everything from hanging out in the studio; going to school was more of a formality. I'm sure nowadays, as the competition has grown, it's important for would-be engineers to look at going to a school because studios have become pickier as to who they're going to let walk through the door. If I was to walk through the door of a studio today – being in the same situation I was in back then, knowing nothing – I would be turned away at the door. There are many people who have some basic learning on the subject that would be much better suited as an intern than I was. I benefited from the era in which I came through the system.
What are the advantages these days of mixing at your home studio or an outside studio?
I don't rent out my own studio. I built it in the basement and only do my own work there. Mixing at home is a double-edged sword. One advantage is that I am home and a client doesn't have to worry about a clock rolling or studio time and accruing a bill. That allows me to take some projects that wouldn't normally have the budget for a bigger studio, since they would have to pay for the studio and then me on top of that. On the negative side, my dogs are here and my wife is here, so it is easy to get distracted sometimes. But I keep focused.
Working with Elton John, who has made 30 studio albums, what have you learned?
Elton is a different beast than anyone else that I've worked with. He writes in the studio – which is not necessarily unique by itself – but when he writes, he will sit down and write a complete song within 30 minutes; start to finish. A complicated song. Generally, I find that the faster he writes a song, the better it is. He gets in this zone, and it's amazing to watch. Sometimes it gives me goosebumps watching him work. I've been working with him 25 years, and it was the same back then as it is now. Even when he wrote the early hits, he'd be done in about 30 minutes and then he'd say, "Okay, let's start rehearsing." He brings his band in right away, they start working out arrangements, and then we begin getting takes. Usually we don't get past three takes before we find the one that works. He is not someone to belabor a process. When it's right, he knows it's right and he moves on. I might have to punch the drums here, or the bass or piano in there, but a lot of times we don't even do that. It's a solid take, start to finish. Then we start overdubbing from that core. With analog we had limited space, and often different parts would have to share the same track – a background vocal filling the space where a lead guitar wasn't. With Pro Tools the options are so unlimited that often you can spend almost all your time trying to sort through what you have with so many parts and takes recorded. But with Elton, once he hears what he wants, he moves on. We're not comping takes together or analyzing one bar versus another. If that's the take, it's the take.
He makes that determination from the feel while playing, or does he listen back?
Sometimes he listens on headphones while sitting at the piano. But, ultimately, he will always come in and listen back on the main speakers in the control room.
Does he know what types of mics he wants? Does he care about that?
Somewhere in between. He leaves that up to me; he trusts that I will make the right decisions for microphones. He has come in before and said, "Is this the same mic we used last year?" which lets me know he liked the sound. He's not naming specific models. His concentration is on performance, and my job is to capture it.
What are some of your favorite vocal mics?
I have a Telefunken [Ela M] 251 that I love. I love [Neumann] U 47s, vintage [AKG] C12s, [Neumann] U 67s, and [Shure] SM7s. I've used all of those with Elton's vocals before. Those are all amazing vocal microphones. I will switch it up sometimes depending upon the song, if it needs a more mellow tone or a brighter sound – depending on the character of the tune. I try to find the nuance and the best fit.
What rack gear do you tend to lean on the most?
I love the old Neve mic preamps; give me a rack of 1073s and I am a happy kid. Some good [Empirical Labs] Distressors, [Universal Audio] 1176 compressors, and some [Teletronix] LA-2As and I'll be able to make a record. It's more about the matter of time rather than the quality of the gear. I lean on the gear that I know I don't have to fight to get a sound that I want. It's my job to be quick, get the band at their creative peak, and keep the energy up. The more time that I spend fiddling with gear, the less time I have dealing with the band. Those pieces of gear; I know what they are going to sound like. I know what they can give me every single time; so if I have them available, I can work extremely fast and I don't have to worry about those aspects.
In what ways has your approach to sound changed and matured over the decades?
Early on, I was very much a gear head. I believed the secret sauce was in this piece of equipment or that microphone. I think it was a period that I had to go through to learn the gear, the studio, and the different characteristics. As I've moved along in my career as a producer, it has become more about the song than the gear, and more about the energy in the room. I don't care how well stocked a studio is, or how pristine the recording is; if it's a bad song, it is a bad song. You're only going to be getting a strong recording of a bad tune. [laughter] There is nothing that you can do. The perfect microphone or preamp is not going to make that song into a hit. I've stopped worrying so much about what piece of gear or what microphone I use, and instead I make sure that I am ready to get the perfect take. When we record guitars, I will usually have a ribbon mic up and a dynamic mic, so I have options to switch between the two. I don't use them both at the same time, usually, but I am prepared to go either way. There have been times when I would prefer one over another for a take, but the one I want is acting up and the guitarist is ready to go, so I don't worry about the mic at that point. It's more important for me to capture the band when they're ready. One of the biggest growing points that I had to get past was focusing so much on my [technical] end. But I had to go through that, and over time I have gained a better understanding of the particular priorities of each project.
What about the current recording zeitgeist irks you most?
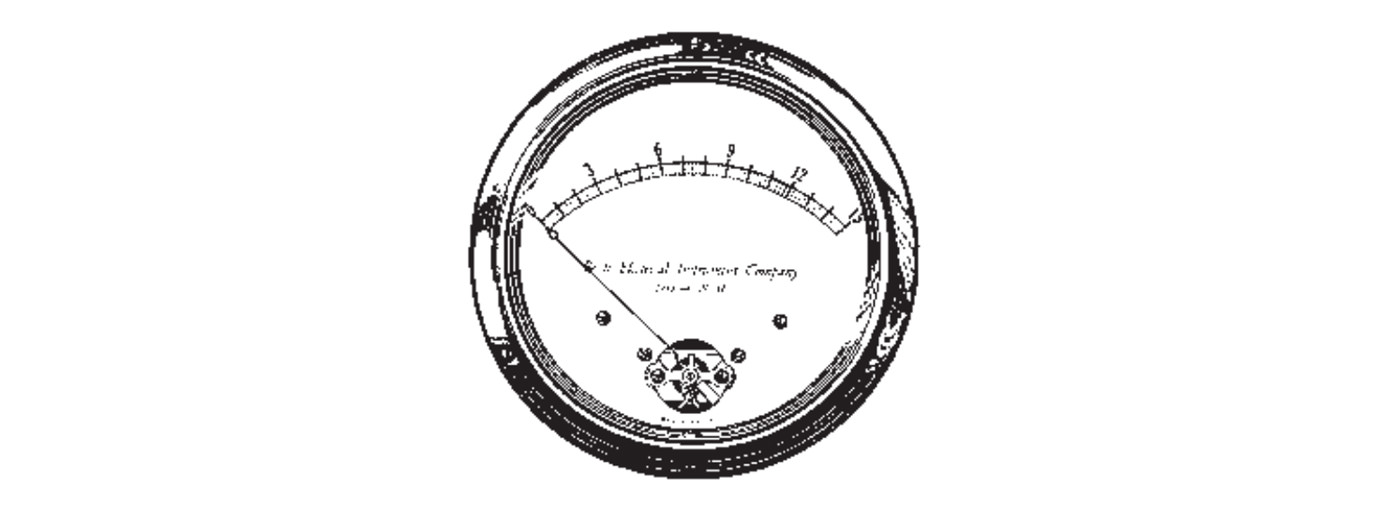
The loudness wars – the over compression, over limiting – makes my ears curl a little bit. But I think that escalation is getting a little bit under control now. Many times, I will hear tracks that are dynamically crushed. It doesn't allow the music to breathe. This could be me holding onto the sound of when music became important to me, and when I chose it as a career. Music never seems to get better than the period when we realized how important it was to us. When I was growing-up I was always listening to Led Zeppelin, The Who, Pink Floyd, Rush, and Jeff Beck. That is the tail I was always chasing. But music has moved on. Sound is perception. How did the drums sound on a record you totally loved? That's probably what you are trying to capture, initially. Over-compression has snowballed since younger groups grew up with that sound and want to repeat what they know and like, but even more intensely. I wish the bands would allow more air and more dynamics. Soft isn't bad. [laughter] Without softness, there is no loudness. You need both ends of the spectrum.
"Hey Ya!" by OutKast is one of those songs that transcends genre boundaries and is timeless. How did that come about?
OutKast do write in the studio, but the songs take more of an evolution. Songs develop over days or weeks into what they are. André 3000 [André Benjamin], Big Boi [Antwan Patton], or whoever is there will be there working for most of the day and listening very loudly. Sometimes they find the hook first, other times the verse. There is no real formula with them, in my experience, but they always try to grow musically, which is one thing that I find refreshing. At one point, André learned to play guitar and then piano – after he was already successful – and he has developed into an even broader musician over time.
You've worked on a diverse range of music. What do you see as the through-line in approaching all of them?
It's all music. Artists are artists, whether it's metal, jazz, country, or pop. There is an underlying love of music; that is the common thread. As long as we are all there for the song we have the possibility of coming out with something special, and I try to maintain that integrity through every session: Serving the song.
You were born and raised in Atlanta. What have you seen as its grown into such a major music center?
The early-1990s was a bit of a heyday for Atlanta. We had LaFace Records – Antonio "L.A." Reid and Kenneth "Babyface" Edmonds' label under Arista – and that's what helped put Atlanta on the map in terms of R&B and hop-hop. You had TLC, Toni Braxton, Arrested Development, and OutKast all coming up. There was a little bit of a slump when L.A. Reid moved to L.A. to run Arista, but now its surged back and we have even more diversity. We've got country with Zac Brown [Band] and Sugarland. There's metal with Mastodon. There's a great jazz scene here now, and, of course, lots of hip-hop. Georgia has a very rich musical history, like James Brown and Little Richard being from Macon, Georgia.
Otis Redding, too.
The history of the state is a lot deeper than many people realize.
Beyond Elton John and OutKast, you've worked with some massive stars, such as Rod Stewart, Lady Gaga, B.B. King, Charles Aznavour, and Carlos Santana. What is your approach to dealing with ego?
The issues are not with the people you might think. The established artists have been around long enough that they value having a good team around them and they tend to demonstrate a lot of respect. Every one of the people you mentioned were a pleasure. The real trouble comes with the new artists, who come in without perspective and think they are the "next big thing." As a producer, you have to realize that they must be there for a reason and it is your job to get that out of them, somehow. I sometimes have to establish a boundary and an understanding of where the responsibilities lie with each person in the room. I've never walked out of a session. I've come close a few times, but those were all with artists that were very new and very green. How you handle artists is different from band to band. Some groups, you have to stroke the ego to reach them. Others, I have to kick their ass and say, "This is shit," and get them almost angry. I'm part producer and part therapist. Get them in their proper headspace and then keep them there. There was one band that only played well when they were fighting. When they were all happy and getting long, they sucked. [laughter] They needed the angst, so in their case we had to let the strife happen and go with it.
How has your classical training benefited you?
It allows me to speak a musicians' language or to read a chart if someone brings in a chart. I can say, "Instead of C major here, maybe try A sharp major," rather than saying, "Try going… lower." It's highly beneficial to have a music background. It's not a requirement, but it helps. There are a lot of great producers, though, that can't play a note but have a wonderful ear.
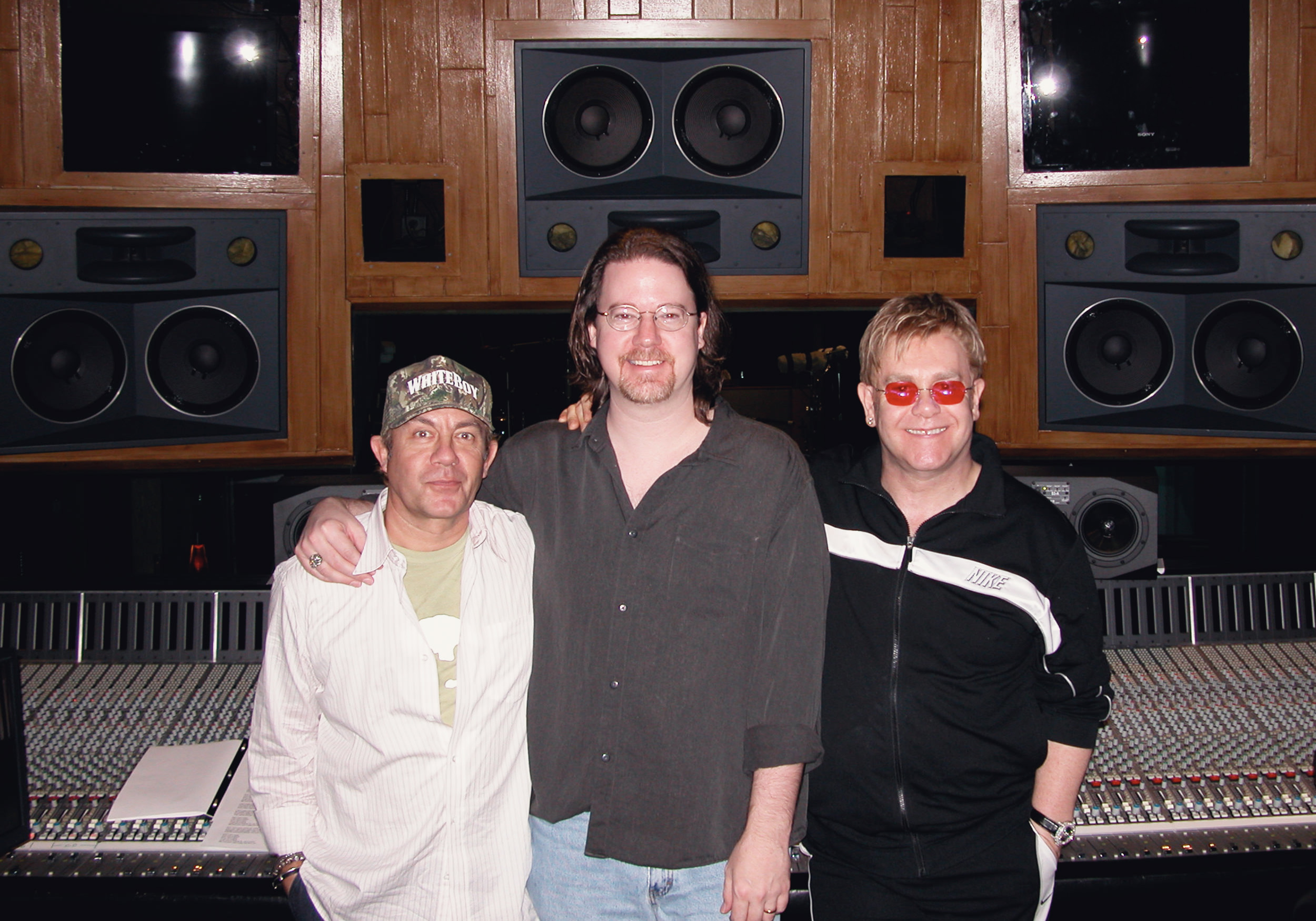
What is your process for mixing?
Whatever the genre is, I start with the foundation. For rock, I will focus in on the guitar, bass, and drums. I work on each part and then start tweaking the blend as they work together. I try to focus on what's the "star" at each point of the song. Obviously, in pop music the vocals are always the star when they are in, but there might be moments between vocal lines where the guitar or a bass note peak through. You have to find those moments that allow for some dynamics to shine, and for each artist to have their moment. Relating to the song is a bit of a process. There are times where I will stop mixing and instead listen to a song six or seven times in a row without doing anything. I might stop mixing for an hour and then come back to it. When I finish a song, I put it to bed and then listen the next day with a fresh set of ears.
Do you listen in different modalities – headphones, cheap speakers, great speakers?
I've got my room so dialed-in that I know it. I used to go out and listen in my car, on my iPhone, and sometimes would play it upstairs on my home system and listen from down the hallway – to hear the mix from as many perspectives as I could. But I do less and less of that than I used to. I am in tune with my room.
What volume do you mix at?
Not very loud. I mix at moderate to soft volume. But then, before printing a mix, I will listen to it at an extremely loud volume. I do want to experience it at different decibel levels.
I've always believed in listening to what pops out or is masked at almost a whisper. You're listening loudly for what it would be like in a club or to catch defects?
More for the volume effect. When you turn something up louder, it invariably seems "better" to you. I do these seminars at universities on the art of listening. I'll present two mixes of the same song. I'll ask the students, "What's the difference between Mix A and Mix B?", and they will come up with, "You added more low end," "You took out the reverb," or, "There's more compression." But the only difference was that the second mix was 3 dB louder. Because it was louder, it sounded better. They always think the louder one is superior. There is a psychology to how loud we listen. When you turn up the volume, the speakers do react differently. Getting louder does change the sound, due to the physics of the speakers. That's why I do listen to a mix loudly, as you never know how someone is going to be experiencing the music – cranking it up or in the background. You want it to sound good no matter what level they are listening to it at.
What are some tips would you give an aspiring engineer?
I tell people not to get stuck with any one way of working. I'm always trying to find new ways. I still pick people's brains to find out how they work. I don't know everything. The second you get stuck thinking that you know everything, you're done. You have to keep up with the technology, especially since it is changing so fast. But also, don't get stuck in technology. Don't get so attached that you can't work without a certain piece of gear. Make music with what you have and make music to the fullest of your ability. It's in you or it's not. The gear is not the magic. Often, I'll walk into a studio, and they will say, "This is the board that this album or that album was made on," and I'm like, "So fucking what?" That board is not the key to that band or their album being iconic. I don't care what albums were made with the gear.
I know some guys who got their hands on a mic that supposedly John Lennon recorded on, and they built their whole musical world around it.
They should put it in a museum, not a studio. [laughter]
www.mattstill.net
Ian Brennan is a Grammy-winning music producer (Tinariwen, The Good Ones, Ramblin' Jack Elliott, Ustad Saami [Pakistan], Zomba Prison Project) and author. In the past decade, Brennan has produced 27 records by international artists from three continents (Africa, Europe, Asia) which have resulted in the first widely-released original music albums from many nations, among them Rwanda, Malawi, South Sudan, and Vietnam. His fifth book, Silenced by Sound: The Music Meritocracy Myth was published in September 2019 by PM Press.